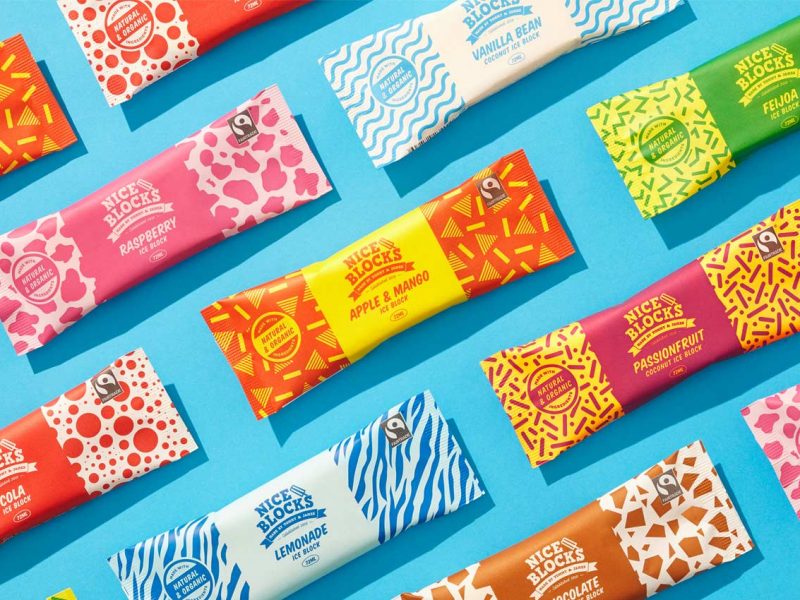
Plastics are currently the most widely used food packaging materials. Because plastic packaging materials are in direct contact with food, the safety of plastic packaging materials and the migration of chemical substances contained in them to food have caused widespread concern.These issues are also an important direction of food safety research.
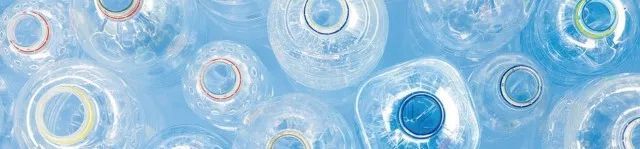
For a long time, the residual and migration of oligomers, harmful monomers, pollutants and additives in solvent-based inks printed on food plastic packaging have been the main aspects affecting the safety of food packaging materials. In order to solve this problem, some new technologies have been introduced into packaging printing, such as ultraviolet (UV) printing technology based on ultraviolet curable inks. Photoinitiators (PIs), as the main components of UV-curable inks, are widely used in the printing of food packaging materials.
After the photoinitiator initiates the polymerization reaction, most of the photoinitiator will become a residue and become the chain end of the polymer, but a small amount of unpolymerized photoinitiator will remain in the ink, and these small molecular compounds can be removed from food packaging. The printing ink of the material migrates into the food, causing food contamination.
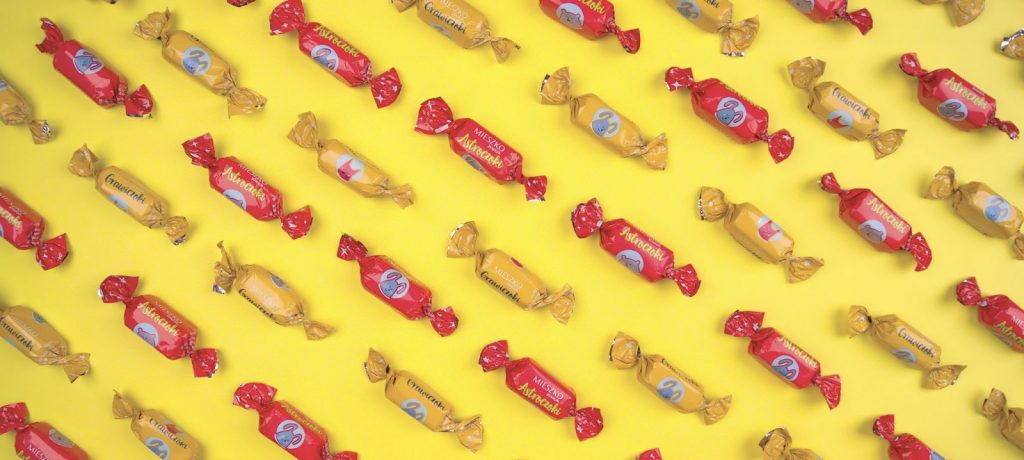
In recent years, studies have found that after the UV ink is cured, the remaining photoinitiator can contaminate the food in the package through chemical migration or physical contact under certain conditions, thereby causing potential hazards to human health.
Since the detection of photoinitiators in Nestlé milk powder in Italy in 2005, the migration and pollution of photoinitiators has attracted attention from all over the world.
In 2007, some researchers found through a mouse toxicology test: Benzophenone (BP) and 4-Methylbenzophenone (PBZ) not only increase the probability of mice suffering from tumors, but also have skin contact. Harm and reproductive toxicity.
In May 2009, the European Commission’s Standing Committee on Food Chain and Animal Health (SCFCAH) stipulated that the specific migration limit of benzophenone in printing inks for food contact materials was 0.6 mg/kg.
In 2015, the European Union Ink Printing Association (EuPIA) clarified the migration restriction requirements of 105 small molecule photoinitiators on the basis of the EU 2002/72/EC document and the Swiss Regulation 817.023.21.

Since food plastic packaging materials may come into contact with many types of food during use, the current exposure assessment of toxic and harmful substances in food plastic packaging materials generally uses food simulants for migration tests. Studies have shown that the properties of food simulants have a significant impact on the migration behavior; polymers of different materials have obvious differences in the migration ability of photoinitiators.
At present, the research on the migration of photoinitiators to foods and food simulants is a hot spot, but there are few studies on the migration laws of photoinitiators in food contact materials to food simulants.
To this end, our researchers selected food simulants according to the national food standard GB/T 23296.1-2009, took the migration process of photoinitiators into food simulants as the research object, and adopted uTo this end, our researchers selected food simulants according to the national food standard GB/T 23296.1-2009, took the migration process of photoinitiators into food simulants as the research object, and adopted ultra-high performance liquid chromatography-tandem mass spectrometry (UHPLC). -MS/MS) Determination of 1-Hydroxycyclohexyl phenyl ketone (SINOCURE 184), benzophenone (SINOCURE BP), 2,2-Dimethoxy-2-phenylacetophenone (SINOCURE BDK), Methyl 2-benzoylbenzoate (SINOCURE OMBB) , Ethyl 4-dimethylaminobenzoate(SINOCURE EDB)etc. in food plastic packaging materials 5 Kinds of photoinitiators, and studied the migration law of these 5 photoinitiators into 3 kinds of food simulants under different migration time and migration materials, providing a basis for the safety assessment of the use of photoinitiators in food packaging materials .
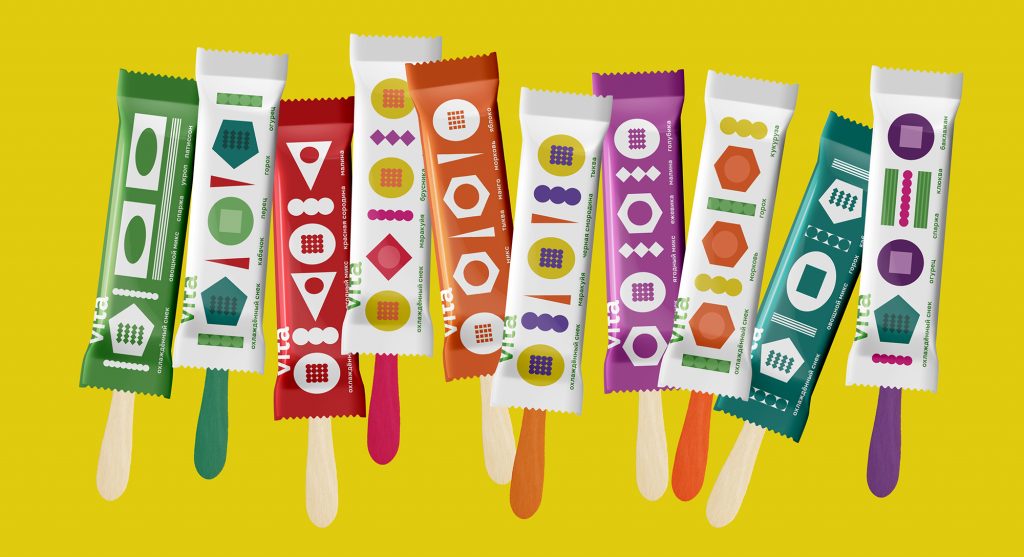
Test
An Agilent Eclipse Plus C18 chromatographic column was used as the separation column, and a mixture of 1g/L ammonium acetate solution and acetonitrile in different volume ratios was used as the mobile phase for gradient elution, and the electrospray positive ion source was used for detection in selective ion monitoring mode. The lower limit of determination (10S/N) of the method is 1.38~5.56μg/dm2. The recovery rate was 77.5%-95.0%, and the relative standard deviation (n=6) of the measured value was 0.81%-8.9%.
- The effect of migration time on the migration of photoinitiators
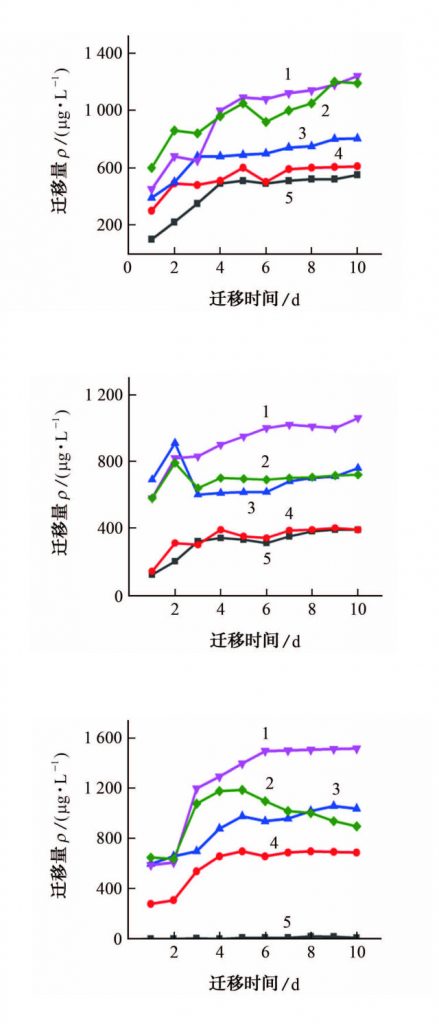
Figure 1- Water;
Figure 2- 10% ethanol solution;
Figure 3- 30g/L acetic acid solution
1-OMBB; 2-EDB; 3-CPK(184); 4-BP; 5-BDK
In three food simulants: water, 10% ethanol solution and 30g/L acetic acid solution, the longer the migration time, the greater the migration amount of the 5 photoinitiators, and the migration amount increased rapidly in the first 5 days. The extended migration volume gradually reaches an equilibrium state.
- The effect of food simulant on the migration of photoinitiators
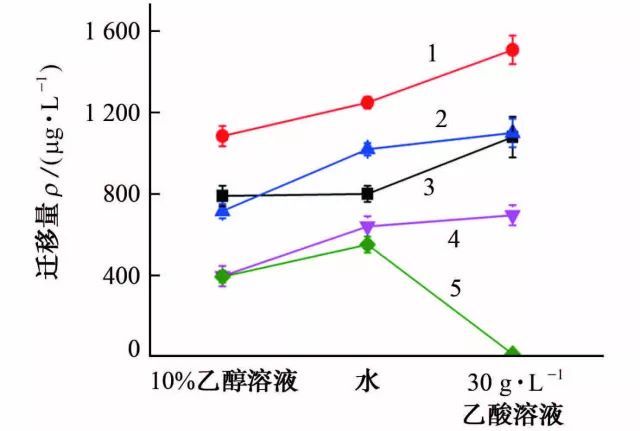
1-OMBB; 2-EDB; 3-CPK(184); 4-BP; 5-BDK
① OMBB has the highest migration amount among the three food simulants, and there are significant differences in the migration amount in different food simulants, and BDK has the least migration amount. The migration amount of 5 kinds of photoinitiators in 3 kinds of food simulants is:
OMBB>EDB>CPK(184)>BP>BDK
② The migration ability of CPK(184) and OMBB in 30g/L acetic acid solution is stronger than that in water and 10% ethanol solution, and the migration ability of EBD and BP in 30g/L acetic acid solution and 10% ethanol solution is higher. Yu Shui. This may be due to the different solubility of the 5 PIs in different food simulants. The solubility of 5 kinds of PIs in water is low, and the migration amount of 5 kinds of PIs in water is the smallest. In a 30g/L acetic acid solution, the migration of BDK is very small, which may be due to the fact that BDK is unstable in acidic solutions and easily decomposes, resulting in a decrease in migration.
- The influence of food packaging materials on the migration of photoinitiators
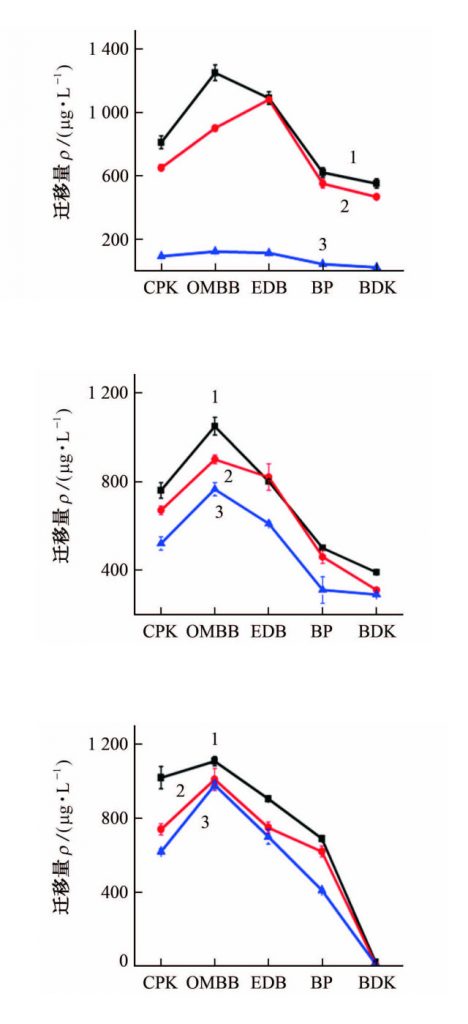
Figure 1-Water;
Figure 2-10% ethanol solution;
Figure 3-30g/L acetic acid solution
1-PE; 2-BOPP/CPP; 3-BOPP/PET/CPP
① In the same kind of food simulant liquid, the migration amount of 5 kinds of photoinitiators in 3 kinds of food packaging materials is:
PE>BOPP/CPP>BOPP/PET/CPP
This may be because the BOPP/PET/CPP material is a three-layer composite, which has good barrier properties, and the photoinitiator is not easy to penetrate into the food simulating liquid, resulting in little migration;
② The barrier ability of BOPP/PET/CPP material to photoinitiator in water is 5-12 times that of the other two food packaging materials, and the barrier ability of BOPP/PET/CPP material in 10% ethanol solution and 30g/L acetic acid solution Only 1.2~1.5 times of the other two materials;
③ There are obvious differences in the migration amount of the same photoinitiator in different food packaging materials. Therefore, the barrier performance is the main factor affecting the migration of the photoinitiator.
- Conclusion
The migration ability of 5 kinds of PIs in different food simulants is different, among which the migration ability to 30g/L acetic acid solution is the strongest; the migration ability of 5 kinds of PIs in different food plastic packaging materials is closely related to the barrier properties of the materials.