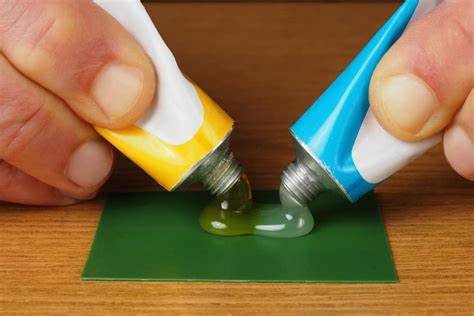
First, the definition of curing agent
The epoxy resin itself is a thermoplastic linear structure and cannot be used directly. The second component must be added to the resin, and the epoxy group of the epoxy resin must be added under certain temperature (or humidity) conditions. It can be used only after forming a polymerization reaction, or catalyzing a polymerization reaction, to generate a cured product of a three-dimensional network structure (body network structure). This compound or resin that acts as the second component is called a curing agent.
The curing agent (Curing agent), also known as the hardening agent (Hardene agent), is an indispensable curing reaction agent for thermosetting resins. The combination of different varieties of resin and curing agent can form cured products with different application methods and different properties, which is a major feature of epoxy resin applications.
- Types and properties of curing agents
There are many kinds of curing agents, and several commonly used curing agents are classified as follows;
- Amine curing agent:
(1) Polyamides: Polyamides as epoxy resin curing agents are prepared by the reaction of dimerized, trimerized vegetable oleic acid or unsaturated fatty acids with polyamine amides. Due to the long fatty acid carbon chain and amino group in the structure, the cured product has high elasticity, adhesion and water resistance, and its workability is also good, the proportion of ingredients is wide, the toxicity is low, and basically no volatile matter , can be constructed on wet metal and concrete surfaces. However, its disadvantage is that the heat resistance is relatively low, and the thermal deformation temperature is only about 50 °C; the curing is not complete below 15 °C, and the physical properties and mechanical properties of the cured product will decrease. Therefore, an accelerator must be added to adjust its curing speed. However, excessive amount will lead to increased brittleness of the cured product; poor resistance to gasoline and hydrocarbon solvents.
(2) Aliphatic amines: The amount of aliphatic amine curing agents is second only to polyamides in various curing agents. This is because most of them are liquid and have good miscibility with epoxy resin; epoxy resin can be cured at room temperature, which is convenient for the process; heat is released during reflection, and the released heat further promotes epoxy resin and curing agent response. Due to the exothermic curing, the amount of epoxy resin used in each batching should not be too much, and the appropriate amount should be mastered according to the specific characteristics of the curing agent. The heat resistance of the cured product is not high, and in order to improve its heat resistance, it can be heated and cured appropriately;
Aliphatic amine curing agents are commonly used in adhesives, sealants, small castings, laminates, room temperature curing coatings, etc.
(3) Aromatic amines: The molecular structure of aromatic amine curing agents contains a stable benzene ring structure, and the amine group is directly connected to the benzene ring. The basicity of aromatic diamines is weaker than that of aliphatic amines, coupled with the steric barriers of aromatic rings, the reactivity with epoxy resins is smaller than that of aliphatic amines; during the reaction with epoxy resins, due to the reactivity of secondary amines and primary amines The difference is very large, the B-stage of the linear polymer solid formed, the re-curing is very slow, and it must be cured by heating. It is advisable to carry out the temperature in stages from low to high during curing.
The cured product has good heat resistance, chemical resistance, electrical properties and mechanical properties.
⑷ Alicyclic amines: Alicyclic amines are amine compounds containing alicyclic (cyclohexyl, heterooxygen, nitrogen atom six-membered ring) in the molecular structure. Most of them are low-viscosity liquids, with a longer pot life than aliphatic amines, and the chroma and gloss of the cured products are better than those of aliphatic amines and polyamides; medium-temperature curing, high price, good transparency, good weather resistance, and high mechanical strength of the cured products; The cured product can be cured at room temperature and used for jewelry glue, which is easy to ripple.
⑸ Polyetheramines: Polyetheramines generally contain a primary amine group connected to one end of the polyether main chain, and the main chain generally has ethylene oxide (EO), propylene oxide (PO) or EO/PO mixed structure, so Named “polyetheramine”.
Polyetheramine cross-linked products can enhance the elasticity, toughness, impact resistance and flexibility of the cured product. Polyetheramine’s low viscosity, low color and long pot life are very suitable for the production and production of epoxy decorative adhesives.
⑹ Imidazoles: Imidazole curing agents are compounds containing imidazole structures in the molecular structure. Imidazole curing agents can cure epoxy resins alone, and can also be used as accelerators for other curing agents such as dicyandiamide, acid anhydrides and phenolic resins.
Compared with other curing agents, the amount of use is small, and epoxy resin can be cured in a short time at medium temperature (80-120 °C). It has a longer pot life and is often regarded as a latent curing agent.
The disadvantage of imidazole compounds is that they have certain volatility and hygroscopicity; many imidazole compounds are crystals with high melting point, which are difficult to mix with liquid epoxy resin, which brings inconvenience to the operation process.
- Acid anhydride curing agent
(1) Aromatic acid anhydrides: Aromatic acid anhydrides contain benzene rings in their molecular structure, and the cured product has good heat resistance, high heat distortion temperature and excellent electrical properties. Because it is a solid, it has a higher melting point.
(2) Aliphatic acid anhydride: Aliphatic acid anhydride is prepared by the interaction of aliphatic dibasic acid and acetic anhydride. Since the molecular structure is an aliphatic long chain, it can impart toughness and thermal shock resistance to the cured resin. These curing agents can be used alone or in admixture with other acid anhydrides as curing agents for powder coatings and casting resins.
(3) Alicyclic acid anhydrides: Alicyclic acid anhydrides are different from aromatic acid anhydrides, and there is no benzene ring in the molecular structure, so the weather resistance of this type of acid anhydrides is better than that of aromatic acid anhydrides.
- Methyltetrahydrophthalic anhydride: Because methyltetrahydrophthalic anhydride has low volatility, low toxicity, and is a low-viscosity liquid, it can be miscible with epoxy resin at room temperature, and its cured epoxy resin has electrical insulation properties. , mechanical strength, heat resistance and other comprehensive properties are good, and the price is relatively cheap, so it is widely used, mainly used for the impregnation of generators, locomotive motor coils, the casting of insulators, insulating bushings, transformers, transformers, TV sets The potting of power transformers makes methyltetrahydrophthalic anhydride one of the most versatile new liquid acid anhydride curing agents.
②, Methylhexahydrophthalic anhydride: Methylhexahydrophthalic anhydride is the product of hydrogenation of methyltetrahydrophthalic anhydride. Compared with Jiasi, Jialiu has the following characteristics:
a. There is no double bond in the molecular structure, and it is colorless and transparent, so it can be used to cast colorless and transparent cured products to produce light-emitting diodes, lenses, laser disks and other products.
b. Due to the relatively non-polar molecular structure, the cured product has good moisture resistance.
c. The thermal deformation temperature of the cured product is high, and the required curing time is short, which is beneficial to the dipping molding of large motors.
d. Since the molecular structure does not contain double bonds, the cured epoxy resin has good weather resistance.
- Latent curing agent
Latent curing agent refers to compounds that have a long pot life in epoxy resins at room temperature and can be rapidly cured by heating or ultraviolet irradiation, and are classified according to external energy. Latent curing agent is a key raw material for preparing one-component epoxy resin adhesives, coatings and casting materials.
Dicyandiamide is the earliest latent curing agent for epoxy resins used in industry. It is a white crystalline powder with a molecular weight of 84, a melting point of 207 to 209°C, and a relative density of 1.40. It is soluble in water and ethanol. Due to the action of the conjugated double bond and the cyano group in the molecule, the basicity of the alkyl-substituted guanidine is greatly reduced, resulting in a relatively long stability between it and the epoxy resin mixture at room temperature; due to the high melting point, the curing temperature is high. The biggest disadvantage is that in order to reduce the curing temperature of dicyandiamide and improve its curing speed, various accelerators are often used together with it.
The cured product of dicyandiamide epoxy resin has excellent adhesion and is not colored, and its dosage has an impact on the properties of the cured product, so it is necessary to choose different dosages according to different uses; In this case, it is better to use a small amount of dicyandiamide.