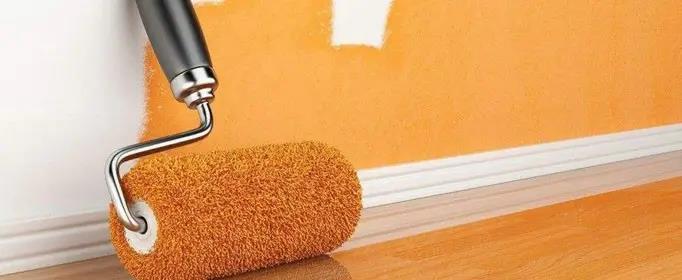
The role and structure type of dispersant applied in coating ink
Coatings are widely used in our daily life for the protection, decoration and special functional role of painted substrates. Coatings are mainly composed of film-forming substances (resins), color fillers, additives and solvents (or water). The pigments applied in coating ink formulations are different from dyes, in that the pigments are usually insoluble in the medium used, and in most cases are present as aggregates. To get good coloring power, covering power and chromaticity, etc., the pigments must be opened up in aggregates and be able to remain stable. If the pigment is not well dispersed, many defects may occur, such as flocculation, loss of light, color shift, floating color, blooming, precipitation, etc.
The form and particle size of pigment. In coatings and inks, pigments are mostly made into suspensions. The particle size range of pigments is wide, generally from 0.05 μm to 1 mm. Research shows that when the particle size of pigment is between 0.05 ~ 0.50 μm, it has *good coloring power, gloss, covering power and weathering resistance (Note: adding suitable UV absorbers to the coating formulation can increase the weathering resistance of pigment).
The *small particles formed during the manufacturing process of pigments are called primitive particles, which exist as a single crystal or a group of crystals with very small particle size. And the agglomerates formed between the primitive particles with face and face junction are called aggregates, which are relatively tight, and it is difficult for the general dispersion equipment to disperse them into primitive particles. And the original particles and aggregates are combined together by van der Waals forces to form larger pigment granular agglomerates, known as epimers. The particles of the attachment are in contact with each other by points, edges and corners, and the inter-particle force is small, so it can be dispersed into original particles or aggregates by mechanical force.
We would like the pigment to be dispersed as a suspension of the original particles (ideal condition), or at least a suspension of the aggregates and the original particles. However, the tendency of the system is to recover from the high energy state to the low energy state, so the pigments distributed as microfine particles tend to aggregate into flocs. Structurally, the flocs are very similar to the aggregates, but it is the resin solution rather than air between the colors in the flocs. The presence of dispersing agents will prevent or slow down the flocculation.
The dispersion process of pigments. The dispersion process of pigments consists of 3 steps: wetting, dispersion and stabilization.
During the wetting process, the air and water vapor on the surface of the pigment is replaced by the resin solution, and the solid/gas phase (pigment/air) is converted into a solid/liquid phase (pigment/resin solution).
Dispersants, especially low molecular type wetting and dispersing agents, can speed up the wetting process. In the dispersion process, mainly relying on mechanical energy (impact and shear), the agglomerated state of the pigment is broken into smaller particles and becomes dispersed (uniform distribution).
The third step is the process of stabilization, the dispersant is used to keep the stability of the pigment dispersion state, to stop the uncontrolled flocculation, and to promote the suspension to obtain a stable state according to the type of binder and molecular structure adsorbed on the surface of pigment. Dispersants, especially polymeric dispersants, play a great role in the stability of pigment particles.
The role of dispersant. Dispersants play a very important role in the production of coatings. The stability of the dispersion system can avoid many coating problems and paint film maladies, if the formulation is reasonable, the right amount of dispersant can effectively reduce costs and improve the performance of coatings.
1、Improve gloss and leveling effect.
2、 Prevent floating color and flowering.
3、 Improve coloring power.
4、 Reduce viscosity and increase pigment loading.
5、 Reduce flocculation and increase workability and usability. Many people do finger study tests when evaluating dispersants. If the dispersant is not properly matched, there will be obvious color difference between the finger study area and the area without finger study, and the pigment coloring power will be reduced after flocculation, which will bring difficulties to color mixing and paint construction. Using flow plate test, can also observe the color paste flocculation or not.
6、Prevent coarsening and increase storage stability.
7、 Increase color spreading and color saturation. Using different dispersants to disperse the same pigment, its color phase and saturation will have obvious differences. Generally speaking, the better the dispersion, the higher the saturation will be (in the case of carbon black, the better the dispersion, the lower the L value, the higher the blackness).
8、 Increase transparency (organic pigments) or coverage (inorganic pigments). For aluminum powder paint, you will want the higher the transparency of the color paste, the better. And for plain paint, you want the higher coverage of the color paste, the better. In fact, this is related to the pigment particle size. According to the data, in addition to refractive index, pigment particle size distribution is another important factor of transparency. As the particle size increases, the ability of scattering light increases until a large value is reached, and then it starts to decrease. This ability to scatter light enhances the covering power of the pigment, which reaches *large when the scattering ability is *strong, and decreases when the particle size continues to increase. When the pigment particle size is below a certain value, the transparency will increase as the particle size decreases. Dispersant can not change the characteristics of the pigment itself, but can control the pigment particle size distribution to achieve a more ideal color effect.
9、Improve grinding efficiency and reduce production cost.
The basic structure and types of dispersants. Dispersant is also called wetting and dispersing agent, it has the function of wetting, one end of its active group can be adsorbed on the surface of the pigment crushed into fine particles, and the other end is solventized into the paint base to form an adsorption layer (the more adsorption groups, the longer the chain link, the thicker the adsorption layer), resulting in charge repulsion (water-based paint) or entropy repulsion (solvent-based paint), so that the pigment particles are dispersed and suspended in the paint base for a long time to avoid flocculation again, thus ensuring This ensures the storage stability of the color paint system.
1、Anionic wetting and dispersing agent. Most of them are composed of non-polar, negatively charged hydrocarbon chains and polar hydrophilic groups. The two groups are at the two ends of the molecule, forming an asymmetric hydrophilic and oleophilic molecular structure. Its varieties are: sodium oleate C17H33COONa, carboxylate, sulfate (R-O-SO3Na), sulfonate (R-SO3Na), etc. Anionic dispersants have good compatibility and are widely used in water-based coatings and inks. Polycarboxylic acid polymers etc. can also be applied to solvent-based coatings and are widely used as controlled flocculation type dispersants.
2、Cationic wetting and dispersing agent. They are non-polar base positively charged compounds, mainly amine salts, quaternary amine salts, pyridinium salts and so on. Cationic surfactants have strong adsorption power and have better dispersion effect on carbon black, various iron oxides and organic pigments, but it should be noted that they react chemically with the carboxyl group in the base material, and also note that they should not be used simultaneously with anionic dispersants.
3、Non-ionic wetting and dispersing agent. They are not ionized in water, do not carry charge, and are weakly adsorbed on the surface of pigment, mainly used in water-based coatings. It is mainly divided into glycol and polyol type to reduce surface tension and improve wettability. Used with anionic dispersants as wetting agent or emulsifier, it is widely used in water-based color paste, water-based coatings and inks.
4、Amphoteric type wetting and dispersing agent.
It is a compound composed of anion and cation. Typical application is the phosphate ester salt type of polymers. These polymers have high acid value, which may affect the interlayer adhesion.
5、Electrically neutral type wetting and dispersing agent. The size of the anionic and cationic organic groups in the molecule is basically equal, and the whole molecule is neutral, but polar. Such as oil amino oleate C18H35NH3OOCC17H33, etc. are of this type, which are quite widely used in coatings.
6、Polymer type hyperdispersant. Polymer type dispersant* is commonly used and has good stability. Polymer type dispersant is also divided into multi-hexane polyol-multi-ethyleneimine block copolymer type dispersant, acrylate polymer type dispersant, polyurethane or polyester type polymer dispersant, etc. Because their anchoring groups are entangled and adsorbed with resin at one end and attached with pigment particles at the other end, the storage stability is relatively good.
7、Controlled free radical type hyperdispersant. Using the new controlled free radical polymerization technology (CFPP), the structure of dispersant can be made more regular. Commonly used methods are: GTP, ATRP (atomic transfer radical polymerization), RAFT (reversible addition breaking chain transfer controlled radical polymerization, including C-RAFT and S-RAFT, etc.), NMP, SFRP (stable radical polymerization), TEMPO, etc. By using controlled radical polymerization technology, the relative molecular mass distribution of dispersant can be more concentrated and the anchoring groups can be more concentrated with higher efficiency.
In order to make the color filler in the coating system fully functional, the application of dispersant and reasonable selection is necessary. Before dispersing pigments, it is necessary to understand the structure of pigments and dispersants. Proper screening of dispersants and addition of the right amount can significantly improve the performance of the coating.