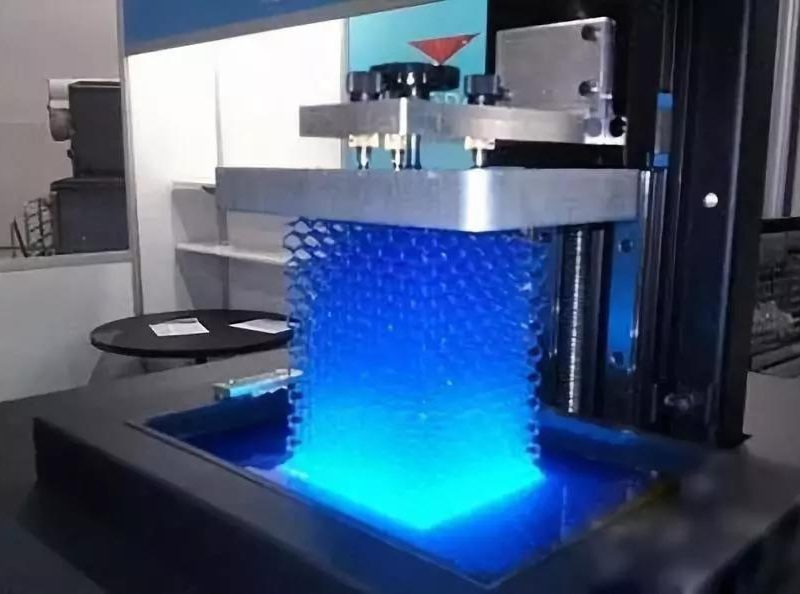
What is the impact and application of post-curing in light-curing 3D printing?
3D printing is an additive manufacturing technology that is completely different from traditional subtractive manufacturing. We can’t talk about 3D printing without mentioning light-curing 3D printing technology.
SLA technology uses a laser beam of ultraviolet light to irradiate a photosensitive resin placed in a pool of material, gradually transforming it from a liquid to a solid to accumulate the final product. Since this curing process requires both the properties of the material itself and the bonding between the cured layers in batches, the curing is usually not very complete and thorough. Therefore, for SLA printing technology, a post-cure is usually required to completely cure the material and improve the physical and mechanical properties of the material. This post-curing technique usually includes UV irradiation, microwave radiation and heating.
Figure 1 Schematic diagram of the SLA technology equipment
The UV laser used has a Gaussian energy distribution, so that the cured product obtained microscopically takes the shape of a bullet, with a certain penetration degree (Cd) and thickness (Lw) (as shown in Figure 2). The determination of Cd and Lw affects the amplitude of the laser scan during curing, as well as the height of the pool lift, and also has a significant impact on the subsequent material properties.
Figure 2 Gaussian distribution of the energy of the UV laser (a), and the resulting bullet-shaped cured material (b)
Due to the parabolic shape of the material obtained with each scan, there are microscopic differences in the cured material obtained after multiple scans, with some parts possibly incompletely cured and some parts over-cured. The uncured parts may shrink at different rates depending on the degree of cure, which can have a significant negative impact on the subsequent processing.
Figure 3 shows the microstructure of three layers of the SLA process with different curing levels.
Another 3D printing technology that is later than SLA technology, DLP is an improvement of SLA technology. Unlike SLA, which uses laser light speed to cure, DLP uses a planar light with a certain shape to light cure the liquid resin, thus reducing the performance differences between different scan lines that exist in SLA technology. Although the problem is mitigated, DLP still suffers from performance differences between different cured layers.
PostCuring becomes particularly important to eliminate the uneven performance, poor dimensional stability, poor dimensional accuracy, and subsequent changes in performance that can occur as a result of the different curing levels that develop during SLA and DLP curing.
The use of ultraviolet light to post-cure the molded material can result in a fully cured layer of several hundred microns on the surface, but not enough curing on the inside due to limited penetration. The post-curing method of thermal curing, on the other hand, can solve this problem very well.
The improvement of anisotropic properties of DLP 3D printing materials was investigated with different thermal initiators, using trithiocarbonates as chain transfer agents, and different thermal post-curing processes.
The materials used in the study were, ethylene oxide pentaerythritol tetraacrylate (40 wt%), trifunctional urethane acrylate Ebecryl8210 (40 wt%), monofunctional urethane acrylate Genomer1122 (20 wt%), photoinitiator TPO (1.0 wt%) and UV blocker MayzoOB+ (0.16%). The thermal initiator used was AIBN (0.4-1.0wt%). The post-thermal curing was performed for 1 hour at 65°C, 90°C, 115°C, or 140°C, respectively.
During the light curing process of 3D printing, the weakening of light penetration caused by the absorption of light by the material leads to a poorer degree of curing the deeper the material is. As can be seen in Figure 4, there is a clear inhomogeneity of the material under SEM and it shows a clear jaggedness at the edges.
Fig. 4 Schematic diagram of the inhomogeneity caused by the weakening of the anisotropic light within the layers that may cause anisotropy (top panel), and SEM images of 3D printed dumbbell-shaped material (bottom panel, printed in vertical direction (left) and horizontal direction (right))
The stress-strain curves of the dumbbell test specimens made by printing in different directions, without UV post-curing, and after 10 minutes of post-curing at 50 mW/cm2 are shown in Figure 5. From the figure, it can be seen that post-UV curing has a significant effect on the performance of the material. The performance of the horizontally printed material is much better than that of the vertically printed material, due to the fact that for vertically printed materials there may be more stress defect points per 50 microns, which leads to a significant reduction in its mechanical properties. After UV post-curing, the material performance is greatly improved, and the gap between horizontally and vertically printed materials is also reduced.
Figure 5 Stress-strain curves for 3D printed materials printed in “horizontal” direction (blue) and “vertical” direction, with and without UV post-curing
The thermal half-life of AIBN as a thermal initiator at 101°C is 6 minutes, so for the post-curing temperature of 60°C to 140°C was chosen. From the results in Figure 6, it can be seen that the performance of 0.4% AIBN at different temperatures does not change much, which means that this amount is not enough to form a significant impact on the performance of the material. And when the dosage to 1%, the effect of thermal post-curing on the performance at different temperatures shows a large difference.
Figure 6 Stress-strain curves of the material at different AIBN dosages and different post-curing temperatures
The plane plots of the response to modulus and stiffness obtained by using temperature and AIBN concentration as the horizontal and vertical axes, respectively, show that the highest modulus is obtained for the case where both concentration and temperature are the highest (Figure 7, left panel). And the rigidity is highest at 140°C regardless of the AIBN concentration (Figure 7, right panel). For the high stiffness at low concentration is due to its greater elongation, while the high stiffness at high concentration is due to its higher modulus.
Based on the above tests, it is known that 1.0 wt% of AIBN and 1 hour of post-heat curing at 140°C has the greatest effect on acrylate conversion because of the greatest increase in its modulus.
Figure 7 Response planes of the material for different AIBN dosages and different post-curing temperatures, modulus (left panel) and stiffness (right panel)
To further investigate the effect of UV post-curing as well as thermal post-curing on the materials, both the materials with and without AIBN (1 wt%) added were first light cured and then thermally cured, and the resulting stress-strain curves are shown in Figure 8. From the figure, it can be seen that for the horizontally printed material, whether AIBN was added or not did not have a great effect. For vertically printed materials, the effect is much greater with or without AIBN. Moreover, even with the addition of AIBN, the performance of the vertically printed material is still weaker than that of the horizontally printed material after two post-cures. This suggests that the addition of AIBN can effectively reduce the anisotropy of 3D printed materials, but this anisotropy is still present. It is possible that this performance is related to the jagged structure present in the vertically printed material described earlier.
Figure 8 Stress-strain curve of the material after simultaneous UV post-curing (50 mW/cm2 irradiation for 10 minutes) and thermal post-curing (140°C heating for 1 hour)
From the above work we can see that since 3D printing is done point by point or surface by surface using point or surface light sources, and the light itself becomes weaker with the depth of the material due to the penetration ability, the curing ability also decreases, which leads to anisotropy in the internal structure of the 3D printed material. This anisotropy can be slightly improved by UV post-curing, but it is very limited. The anisotropy can be greatly improved by using thermal post-curing. Post-curing with 1.0 wt% AIBN at 140°C helped the most in modulus improvement. However, there is still a 15% difference between the modulus of materials printed horizontally and vertically under the same post-curing conditions, which indicates that anisotropy still exists. More research and exploration work needs to be done to completely eliminate anisotropy in 3D printed materials.