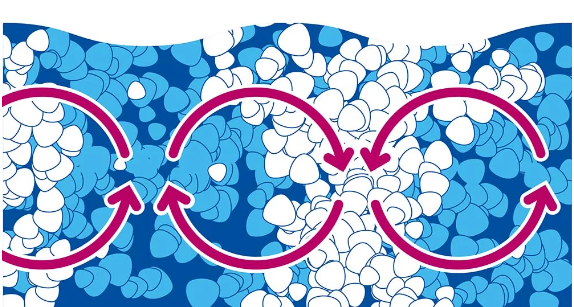
Benard convection, also known as Rayleigh-Benard convection, is a natural convection that occurs in a horizontal fluid layer that is heated from below and cooled from above. The phenomenon is named after Henry Benard, who first observed and studied it in the early 20th century.
The basic principle of Benard convection is the interaction between buoyancy and viscous forces in a fluid layer. When a fluid layer is heated from below, the lower part of the fluid becomes less dense due to thermal expansion. The less dense fluid tends to rise while the cooler fluid with a higher density in the upper part settles downward, resulting in a convective pattern.
When the temperature difference exceeds a critical value, the fluid becomes unstable and convective cells or vortices begin to form. These vortices are characterized by a hexagonal or roll shape, with the fluid rising in the center of the cell and falling along the cell boundary, creating a circular motion. The size and shape of the convection cell depends on a number of factors, including the nature of the fluid, the temperature difference between the bottom and top surfaces, and the depth of the layer.
As the Rayleigh number increases further, the convection pattern becomes more complex and may undergo various transformations leading to different flow regimes. These transformations are usually accompanied by changes in cell structure, such as the formation of smaller cells within larger cells (known as “wind-hexagonal” modes), or the appearance of oscillatory or chaotic behavior.
The formation of Bernard vortices can lead to a variety of phenomena, such as
- Uneven drying or curing of coatings or films, leading to surface defects and inhomogeneities.
- Interference in the heat transfer process, affecting the efficiency of systems such as heat exchangers or solar collectors.
- Pattern formation and self-organization of various materials, including thin films, liquid crystals and granular materials.
Benard convection effects can have a significant impact on the surface of paint coatings, especially if there is a temperature gradient across the coating during the drying or curing process. The formation of convection chambers can lead to uneven drying, surface defects and potential coating quality degradation. The following are some strategies for mitigating or resolving the effects of Benard eddy currents on painted coating surfaces:
- 1. Control Temperature Gradients: One of the main factors driving Benard convection is the temperature difference between the bottom and top surfaces of the coating. By minimizing the temperature gradient, the driving force for convection can be reduced or eliminated. This can be accomplished by
- a. Adjusting the curing or drying temperature to maintain a more uniform temperature throughout the coating layer.
- b. Using insulation or heating/cooling systems to maintain a consistent temperature across the coating surface.
- c. Optimize coating thickness to minimize temperature gradients within the coating.
- 2. Modify coating rheology: The rheological properties of the coating material (e.g., viscosity and viscoelasticity) affect the formation and stability of the Benard convection cell. Increasing viscosity or introducing viscoelastic additives can inhibit convection and suppress vortex formation.
- 3. Use of Surfactants: Certain surfactants, such as surfactants or leveling agents, can alter the surface tension of the coating and disrupt the formation of convection cells. These additives help to create a more uniform surface during drying or curing.
- 4. Adjusting the coating application method: The way the coating is applied can also affect Benard’s sensitivity to flow. Continuous, uniform application techniques such as spray or curtain application may be less susceptible to convection effects than brush or roller application methods.
- 5. Optimize drying or curing conditions: The speed of drying or curing affects Benard convection. Fast drying or curing minimizes the time window for convective cell formation and stabilization. However, too fast drying can also lead to other defects, so a balance must be struck.
- 6. Introduce vibration or agitation: Slight vibration or agitation of the coated surface during the drying or curing process can disrupt the formation of stable convective holes and result in a more uniform surface.
- 7. Use of Multi-Layer Coating Strategies: In some cases, the use of multiple thin layers of coating during intermediate drying or curing steps can help mitigate the Benard convection effect by reducing the overall temperature gradient and minimizing the time it takes for convection chambers to form.
AgeSin® Coating and Ink Additives series product introduction
We have: polyacrylate leveling agents; fluorocarbon-modified polyacrylate leveling agents; polyether-modified silicone leveling agents; fluorosurfactants; polyester-modified silicone leveling agents; anti-graffiti additives; performance enhancers.
If you would like to shop our range of AgeSin® coatings and ink additives, you are welcome to click on the links below to view specific options.
How to solve the wettability, fluidity and leveling of the coating surface in Paints/Inks
Contact Us Now!
If you need MSDS,TDS or sample testing, please email us at info@sinocurechem.com or use the website live chat to get prompt reply.