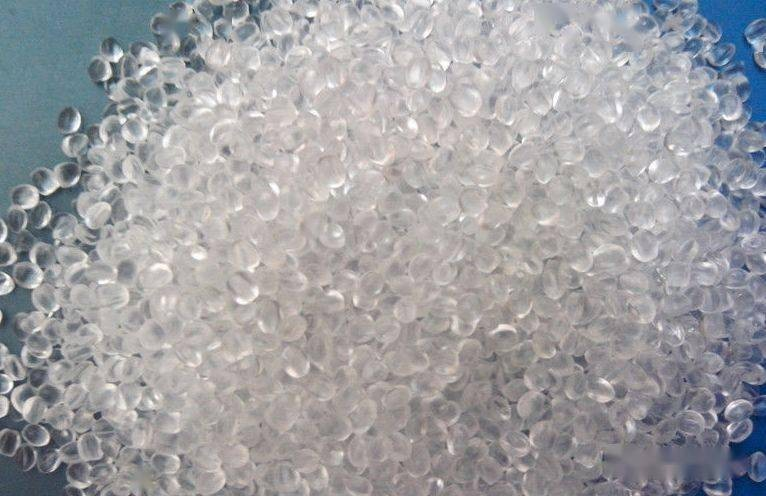
Components of EVA
What we call photovoltaic material EVA, refers to the VA content of 25% – 40% of ethylene, vinyl acetate copolymer, EVA is a hot melt adhesive, non-tacky and anti-adhesive at room temperature, in order to operate, after a certain condition of hot pressure will occur melt bonding and crosslinking curing, and become completely transparent, cured EVA and glass bonding to improve the light transmittance of the glass, play a role in increasing the transparency of the solar cell module output. EVA thickness between 0.4mm ~ 0.6mm, flat surface, uniform thickness, containing crosslinking agent, can be crosslinked at a curing temperature of 150 ℃, using extrusion molding process to form a stable adhesive layer.
EVA has excellent flexibility, impact resistance, elasticity, optical transparency, low-temperature bending, adhesion, environmental stress cracking resistance, weather resistance, chemical resistance, heat sealing.
The properties of EVA depend mainly on the molecular weight (expressed by the melt index MI) and the content of vinyl acetate (expressed as VA). When the MI is constant, the elasticity, flexibility, adhesion, compatibility and transparency of VA increase, and when the content of VA decreases, the properties are close to those of polyethylene.
When the VA content is certain, the softening point decreases when the MI decreases, and the processability and surface gloss improve, but the strength decreases, and the molecular weight increases, which improves the impact resistance and stress cracking.
The effect of VA content of EVA on the material itself: EVA is a thermoplastic resin produced by copolymerization of ethylene and vinyl acetate. The vinyl acetate (VA) content of industrial products ranges from 5% to 95%, and as the VA content increases, the EVA becomes softer. the softness of the EVA will affect the fragmentation of the component layup.
Classification of VA content
- VA content of 5% to 15% of EVA: suitable for agricultural film, packaging film, cable sheathing, etc..
- VA content of 15% to 40% of EVA: shoe soles, sealing strips, foam and so on. With many materials have good bonding properties, can be made into a variety of hot melt adhesive.
- VA content of 40% to 70% of EVA: plastic processing modifier.
- EVA with VA content of 70% to 95%: sold in the form of emulsion, used to formulate various paints, adhesives and used as paper and fabric coatings.
Different temperatures have a greater effect on the degree of adhesion of EVA, which directly affects the performance and service life of the components. In the molten state, EVA is bonded to crystalline silicon solar cell wafers, glass, and TPT, in a process that involves both physical and chemical bonding. Unmodified EVA is transparent, soft, has hot melt adhesion, low melt temperature and good melt flow. However, its heat resistance is poor, easy to extend and low elasticity, low cohesive strength and poor creep resistance, prone to thermal expansion and contraction leading to chip fragmentation, making the bonding delamination.
Therefore, by taking the chemical crosslinking of EVA modification, the method is to add organic peroxide crosslinking agent in EVA, when EVA is heated to a certain temperature, the decomposition of the crosslinking agent generates free radicals, triggering the combination between the EVA molecules, the formation of three-dimensional mesh structure, resulting in the crosslinking and curing of EVA adhesive layer, when the degree of crosslinking reaches 60% or more can withstand atmospheric changes, no longer occurs! Heat expansion and cold contraction no longer occurs.
The influence of cross-linking degree on components
According to theoretical analysis, the higher the degree of crosslinking, the higher the transmittance of EVA, the higher the overall output power of the component, after the lamination process to adjust the parameters of the crosslinking degree of EVA can reach a maximum of 95%-98%, but the higher the degree of crosslinking in the application process to produce the chance of cracking the greater the degree of crosslinking of EVA is on the low side of the degree of de-lamination with the glass, the backplane, resulting in internal circuitry with the decline in its own mechanical properties. At present, many manufacturers suggest that the crosslinking degree range of about 85% is the best.
EVA’s ultraviolet cut-off wavelength on the impact of the component: the intensity of the sun’s distribution: 0.7nm-280nm is not easy to reach the earth, 280nm-400nm for the UV ultraviolet, 400nm-750nm for the visible light, 750nm-3000nm for infrared. Currently in contact with the EVA, (Foster F406 belongs to the low cut-off UV products) other manufacturers of UV cut-off wavelengths are in 360nm-380nm, which itself has a certain cut-off of ultraviolet light.
The UV cutoff of EVA mainly relies on the UV absorber of EVA itself to absorb the UV light and convert it into heat energy and emit it, and the part of EVA itself that turns yellow is the internal coupling agent, antioxidant, bridging agent and other qualitative changes. However, there is no detailed data on the lifetime of the UV absorber.
Cross-linking reaction of EVA
EVA (Ethylene Vinyl Acetate Copolymer) film: It is a thermosetting hot melt adhesive that undergoes a cross-linking reaction when heated to form a thermosetting gel resin.
EVA film is a linear macromolecule before lamination. When heated, the cross-linking agent decomposes to form reactive free radicals, which trigger the intermolecular reaction of EVA to form a mesh structure. This improves the mechanical properties, heat resistance, solvent resistance and aging resistance of EVA.
The main composition of EVA and the impact on its performance
EVA film mainly consists of: EVA body, crosslinking agent system (including crosslinking initiator and crosslinking agent), polymerization blocking agent, heat stabilizer, light stabilizer, silane coupling agent and other components.
Common ways of EVA failure
- Yellowing: EVA yellowing caused by two factors (mainly additives system mutual reaction yellowing; secondly, the EVA molecules in the oxygen, light conditions, the EVA molecules of their own deacetylation reaction resulting in yellowing), so the EVA formula to determine the anti-yellowing performance of its good or bad.
- Bubbles: Bubbles include two kinds, one is: EVA internal components generated bubbles are not pumped out in a timely manner. (EVA additive system, other materials and EVA matching, lamination process are related); another for the poor matching between the materials lead to bubbles after lamination.
- Delamination: delamination with the backing plate (unqualified crosslinking degree, poor bonding strength with the backing plate); delamination with the glass (defective silane coupling agent, dirty glass, unqualified crosslinking degree).
If you need to buy organic peroxide crosslinker products, the following is our product information, welcome to click to view.
Product Name |
CAS NO. |
Chemical Name |
94-36-0 |
Benzoyl peroxide;Dibenzoyl peroxide |
|
80-43-3 |
Dicumyl peroxide |
|
80-15-9 |
Cumyl hydroperoxide |
|
105-74-8 |
Dilauroyl peroxide / Lauroyl peroxide |
|
25155-25-3/2212-81-9 |
Bis(tert-butyldioxyisopropyl)benzene peroxide |
|
25155-25-3/2212-81-9 |
Bis(tert-butyldioxyisopropyl)benzene peroxide |