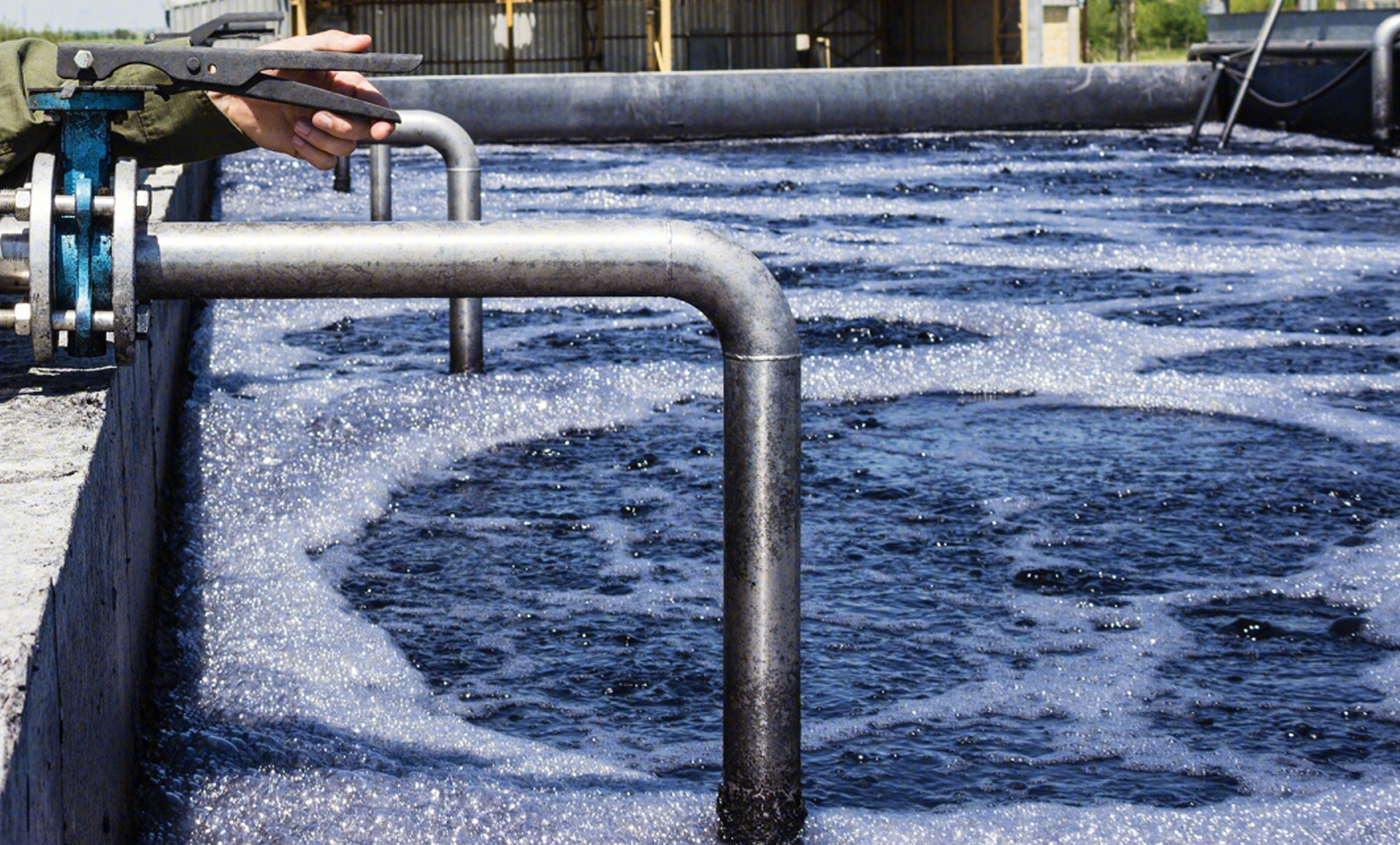
What is Foam
Foams are aggregates of bubbles separated from each other by a liquid film, and are dispersed systems of gases in liquids where the volume fraction of the internal phase (gas) is generally greater than 90%. Foam has many applications in production practice, such as foam separation, foam fire extinguishing. The formation and stability of foam is closely related to surface tension, buoyancy and other physical principles.
Causes of Foam Generation
Foam generation requires gas-liquid contact. This consists of two situations: first, the gas enters the liquid from the outside, such as mixing the gas when stirring the liquid. The second is that the gas is generated from inside the liquid, such as boilers, evaporators, etc. when the temperature rises part of the liquid gasification, or oil recovery and transportation in the pressure changes in the escape of gas.
Why defoaming
Improve efficiency: In many industrial processes, such as the chemical industry, oil extraction, paper, printing, dyes, paints, plastics, etc., large quantities of foam can affect productivity. These foams may hinder the normal operation of machines and reduce productivity, so defoaming is needed to reduce foam generation and ensure the smooth running of the production process.
Ensure product quality: In the food and beverage industry, foam generation may affect the taste, appearance and quality of the product. For example, in the production of beer, fruit juices, dairy products, etc., excessive foaming may lead to a decrease in product quality. Therefore, antifoam agents are used to control the formation of foam and bubbles to maintain product stability and quality.
Improve drug quality: In the pharmaceutical manufacturing process, such as mixing, blending and filtration of drug solution, the generation of air bubbles may affect the stability and effectiveness of the drug. The addition of defoamer can effectively inhibit the generation and stabilization of air bubbles, improve the quality of the drug and the accuracy of filling.
Effective in agriculture: Agricultural silicone defoamers can quickly destabilize foams and prevent their formation, which can help reduce problems such as pests and algal blooms in crops.
Saving energy and costs: In some defoaming methods, such as thermal defoaming, the foam is broken up by heating. Although this method may consume a certain amount of energy, in the long run, energy and cost savings can be realized by reducing equipment maintenance costs and energy consumption through the reduction of foam production.
Defoaming Mechanism
Antifoam agent has low surface tension, so it is easy to enter and expand into the liquid film, reducing the surface tension of the liquid film, making the liquid film gradually thin, uneven internal force, and losing self-repairing ability, thus leading to its rupture.
Classification
- Silicone antifoam agent has a lower surface tension than water, surfactant aqueous solution and general oil, and at the same time has low volatility and chemical inertia. These characteristics make it has a strong antifoaming performance and rapid bubble breaking ability, applicable to a wide range.
- Surfactant defoamer is actually an emulsifier, using the dispersing effect of surfactant to disperse the foam-forming substances in the water, so as to avoid generating foam. It has the advantages of easy availability of raw materials, high environmental performance and low production costs, but the defoaming efficiency is low and specialized.
- the biggest advantage of polyether antifoam agent is strong foam inhibition ability, and at the same time, it has the characteristics of high temperature resistance, strong acid and alkali resistance. Therefore, in some harsh environments can also achieve the purpose of continuous defoaming and foam inhibition. But by the temperature limitations, defoaming efficiency is low, the use of the field is not as extensive as the silicone class.
- Mineral oil antifoam agent can play a role in acidic and alkaline conditions, and at the same time has good heat resistance. However, the compatibility of such defoamer is poor, for intensive foam effect is not good, not for the product appearance of the strict requirements of the industry in the gloss, generally used in coatings and inks for those who do not require a high level of gloss in the process.
Applications in particular industries
Defoaming is crucial in various industries, each with specific requirements:
a) Food and Beverage:
Used in dairy processing, brewing, and fruit juice production
Helps maintain product quality and consistency
Often requires food-grade, non-toxic defoamers
b) Wastewater Treatment:
Controls foam in aeration tanks and digesters
Improves efficiency of treatment processes
Requires environmentally friendly defoamers
c) Pulp and Paper:
Used in pulping, bleaching, and coating processes
Prevents overflow in tanks and improves drainage on paper machines
Often requires defoamers resistant to high temperatures and pH variations
d) Oil and Gas:
Controls foam in drilling fluids and during gas sweetening
Improves efficiency of separation processes
Requires defoamers stable under high pressure and temperature
e) Pharmaceuticals:
Used in fermentation processes and drug formulation
Helps maintain sterility and product purity
Requires highly pure, non-reactive defoamers
f) Textile Industry:
Controls foam in dyeing and finishing processes
Improves fabric quality and process efficiency
Often requires defoamers compatible with various dyes and chemicals
g) Paint and Coatings:
Prevents foam during manufacture and application
Improves surface finish quality
Requires defoamers compatible with different paint chemistries
Below you will find our range of defoamers, click to view them now!
Product Name | Alternative models | Chemical Name |
AgeSin® DF-D952R | Acrylate copolymer solution | |
AgeSin® DF-D912R | BYK-141; BASF EFKA 2018;ELEMENTIS Defom 5300 | Fluorine modified organic silicon polymer solution |
AgeSin® DF-D9904B | Tego Airex 904W | Polyether siloxane copolymer, without SiO2 |
AgeSin® DF-D9901 | Tego Airex 901W | Polyether modified polysiloxane compounds, containing SiO2 |
AgeSin® DF-D9202 | Tego Airex 920 | Modified polysiloxane |
AgeSin® DF-D955R | BYK 055 | Foam-breaking polymer liquid with silicon-free |
AgeSin® DF-T2030 | BYK-1788 | Non-silicone high molecular weight polymer for breaking foam. |
AgeSin® DF-D982V | Tego Airex 900;Tego Foamex N;Shin-Etsu KS66 | Polysiloxane compound with hydrophobic particles |
AgeSin® DF-D980 | Tego Airex 900;Tego Foamex N;ELEMENTIS Defom 6800 | Polysiloxane compound with hydrophobic particles |