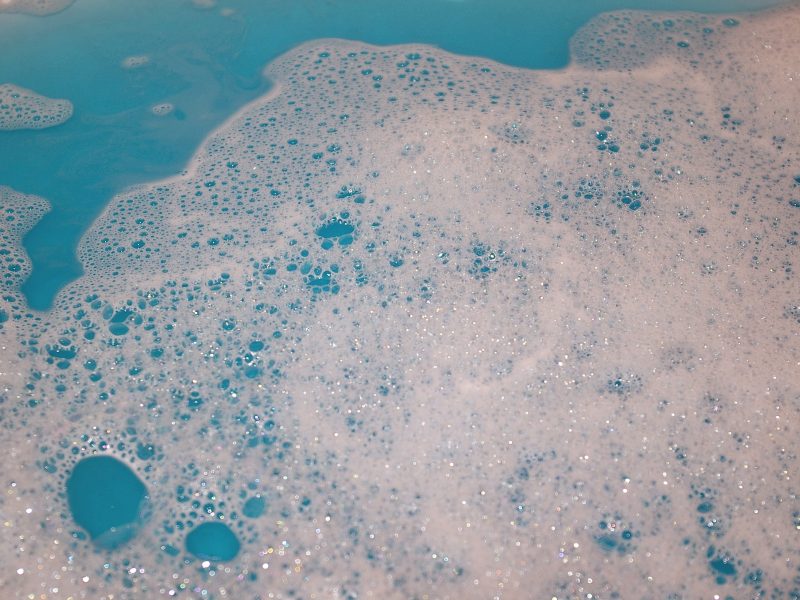
1. Methods for eliminating foam
1) Physical methods
From a physical point of view, the methods for eliminating foam mainly include placing baffles or filters, mechanical stirring, static electricity, freezing, heating, steam, radiation, high-speed centrifugation, pressurization and decompression, high-frequency vibration, instantaneous discharge and ultrasound (acoustic liquid control), etc. These methods promote the permeation rate of gas at both ends of the liquid film and the drainage of the bubble film to varying degrees, making the stability factor of the foam smaller than the attenuation factor, so that the amount of foam gradually decreases. However, the common disadvantages of these methods are that their use is strongly restricted by environmental factors and the defoaming rate is not high. The advantages are environmental protection and high reuse rate.
2) Chemical methods
From a chemical point of view, the methods for eliminating foam mainly include chemical reaction method and defoaming agent addition method. The chemical reaction method refers to adding some reagents to react chemically with the foaming agent to generate water-insoluble substances, thereby reducing the concentration of surfactants in the liquid film and promoting the rupture of the foam. However, this method has the disadvantages of uncertain composition of the foaming agent and the generation of insoluble substances that harm the system equipment. Nowadays, the most widely used defoaming method in all walks of life is to add defoaming agents. The biggest advantage of this method is that it has high defoaming efficiency and is easy to use, but finding a suitable and efficient defoaming agent is the key.
2. The principle of defoaming agent
Defoaming agent, also known as defoaming agent, has the following principles:
1) The local surface tension of the foam is reduced, causing the foam to burst
The origin of this mechanism is that higher alcohols or vegetable oils are sprinkled on the foam. When they are dissolved in the foam liquid, the surface tension at that place will be significantly reduced. Because these substances generally have low solubility in water, the reduction in surface tension is limited to the local part of the foam, and the surface tension around the foam has almost no change. The part with reduced surface tension is strongly pulled and extended to the surroundings, and finally bursts.
2) Destruction of membrane elasticity leads to bubble bursting
When the defoaming agent is added to the foam system, it will diffuse to the gas-liquid interface, making it difficult for the surfactant with foam stabilization to restore the membrane elasticity.
3) Promote the drainage of liquid film
Defoamers can promote the drainage of liquid film, thus causing bubbles to burst. The rate of foam drainage can reflect the stability of foam. Adding a substance that accelerates foam drainage can also play a defoaming role.
4) Adding hydrophobic solid particles can cause bubbles to burst
Hydrophobic solid particles on the surface of bubbles will attract the hydrophobic end of the surfactant, making the hydrophobic particles hydrophilic and entering the water phase, thereby playing a defoaming role.
5) Solubilizing and foaming surfactants can cause bubbles to burst
Certain low-molecular substances that can be fully mixed with the solution can solubilize the bubble surfactant and reduce its effective concentration. Low-molecular substances with this effect, such as alcohols such as octanol, ethanol, and propanol, can not only reduce the surfactant concentration of the surface layer, but also dissolve into the surfactant adsorption layer, reduce the tightness between surfactant molecules, and thus weaken the stability of the foam.
6) Electrolytes break up the double layer of surfactants
For foaming liquids that rely on the interaction of the double layer of surfactants in foam to produce stability, adding ordinary electrolytes can break up the double layer of surfactants to play a defoaming role.
3. Classification of defoamers
Common defoamers can be divided into silicone (resin), surfactant, paraffin and mineral oil according to their ingredients.
1) Silicon (resin)
Silicone resin defoamer is also called emulsion defoamer. The method of use is to emulsify and disperse silicone resin in water with emulsifier (surfactant) and then add it to the wastewater. Silicon dioxide fine powder is another silicone defoamer with good defoaming effect.
2) Surfactant
This type of defoamer is actually an emulsifier, that is, the dispersion effect of surfactant is used to keep the foam-forming substance in a stable emulsified state in water, thereby avoiding the formation of foam.
3) Paraffin
Parallel defoamer is a defoamer made by emulsifying and dispersing paraffin wax or its derivatives with an emulsifier. Its use is similar to that of emulsified defoamers of surfactant.
4) Mineral oil
Mineral oil is the main defoaming component. In order to improve the effect, metal soap, silicone oil, silica and other substances are sometimes mixed and used together. In addition, in order to make mineral oil easily diffuse to the surface of the foaming liquid, or to make metal soaps and the like evenly dispersed in the mineral oil, various surfactants can sometimes be added.
4. Advantages and disadvantages of different types of defoamers
Mineral oils, amides, lower alcohols, fatty acids and fatty acid esters, phosphates and other organic defoamers were studied and applied earlier and belong to the first generation of defoamers. They have the advantages of easy raw materials, high environmental performance and low production cost; the disadvantages are low defoaming efficiency, strong specificity and harsh use conditions.
Polyether defoamers are the second generation of defoamers, mainly including linear polyethers, polyethers with alcohol or ammonia as initiators, and end-esterified polyether derivatives. The biggest advantage of polyether defoamers is their strong anti-foaming ability. In addition, some polyether defoamers have excellent properties such as high temperature resistance and strong acid and alkali resistance; the disadvantages are that the use conditions are limited by temperature, the use field is narrow, the defoaming ability is poor, and the foam breaking rate is low.
Silicone defoamers (third generation defoamers) have strong defoaming performance, fast foam breaking ability, low volatility, no toxicity to the environment, no physiological inertness, and a wide range of applications. Therefore, they have broad application prospects and huge market potential, but their anti-foaming performance is poor.
Polyether modified polysiloxane defoamers have the advantages of both polyether defoamers and silicone defoamers, and are the development direction of defoamers. Sometimes they can be reused according to their reverse solubility, but there are currently few types of such defoamers, and they are still in the research and development stage, and the production cost is high.
5. Selection of defoamers
The selection of defoamers should meet the following points:
1) Insoluble or poorly soluble in the foaming liquid
In order to break the foam, the defoamer should be concentrated and concentrated on the foam film. For the case of the defoamer, it should be concentrated and concentrated instantly, and for the case of the anti-foamer, it should always be kept in this state. Therefore, the defoamer is in a supersaturated state in the foaming liquid, and only insoluble or poorly soluble ones can easily reach a supersaturated state. Insoluble or poorly soluble, it is easy to gather at the gas-liquid interface, easy to concentrate on the bubble film, and can play a role at a lower concentration. For defoamers used in water systems, the molecules of the active ingredients must be strongly hydrophobic and weakly hydrophilic, with an HLB value in the range of 1.5-3, and the effect is best.
2) The surface tension is lower than the foaming liquid
Only when the intermolecular force of the defoamer is small and the surface tension is lower than the foaming liquid, the defoamer particles can be immersed and expanded on the bubble film. It is worth noting that the surface tension of the foaming liquid is not the surface tension of the solution, but the surface tension of the foaming solution.
3) A certain degree of affinity with the foaming liquid
Since the defoaming process is actually a competition between the foam collapse speed and the foam generation speed, the defoamer must be able to disperse quickly in the foaming liquid so that it can quickly play a role in a wider range of the foaming liquid. In order to make the defoamer diffuse faster, the active ingredients of the defoamer must have a certain degree of affinity with the foaming liquid. If the active ingredients of the defoamer are too close to the foaming liquid, they will dissolve; if they are too sparse, they will be difficult to disperse. Only when the affinity is appropriate, the effect will be good.
4) No chemical reaction with the foaming liquid
The defoamer reacts with the foaming liquid. On the one hand, the defoamer will lose its effect, and on the other hand, harmful substances may be produced, affecting the growth of microorganisms.
5) Low volatility and long action time
First, it is necessary to determine the system in which the defoamer is needed, whether it is a water-based system or an oil-based system. For example, in the fermentation industry, oil-based defoamers should be used; such as polyether-modified silicon or polyether, the water-based coating industry should use water-based defoamers and silicone defoamers. Select the defoamer, compare the addition amount, and refer to the price to obtain the most suitable and economical defoamer product.
6. Factors affecting the use effect of the defoamer
1) Dispersibility of the defoamer in the solution
The dispersion state and surface properties of the defoamer in the solution significantly affect other defoaming properties. The defoamer should have a suitable degree of dispersion and particles with too large or too small particle size will affect their defoaming activity.
2) Compatibility of defoamers in foam systems
When the surfactant is completely dissolved in the aqueous solution, it is usually oriented at the gas-liquid interface of the foam to stabilize the foam. When the surfactant is in an insoluble or supersaturated state, the particles are dispersed in the solution and accumulate on the foam, and the foam acts as a defoamer.
3) Foaming system ambient temperature
The temperature of the foaming liquid will also affect the performance of the defoamer. When the temperature of the foaming liquid itself is relatively high, it is recommended that a special high-temperature resistant defoamer must be used, because if an ordinary defoamer is used, the defoaming effect will definitely be greatly reduced, and the defoamer will directly demulsify the emulsion.
4) Packaging, storage and transportation
The defoamer is suitable for storage at 5-35℃, and the shelf life is generally 6 months. Do not place it near a heat source or expose it to sunlight. According to the commonly used chemical storage method, make sure it is sealed after use to avoid deterioration.
5) Defoamer addition ratio
The addition of the original solution and the addition after dilution have some deviations to a certain extent, and the ratio is not equal. Due to the low concentration of the surfactant, the diluted defoamer emulsion is extremely unstable and will not be stratified soon. The defoaming performance is relatively poor, which is not suitable for long-term storage. It is recommended to use it immediately after dilution.
The proportion of adding defoamer needs to be verified by field tests to verify the effect, and it should not be added excessively.
Below you will find our range of defoamers, click to view them now!
Product Name | Alternative models | Chemical Name |
AgeSin® DF-D952R | Acrylate copolymer solution | |
AgeSin® DF-D912R | BYK-141; BASF EFKA 2018;ELEMENTIS Defom 5300 | Fluorine modified organic silicon polymer solution |
AgeSin® DF-D9904B | Tego Airex 904W | Polyether siloxane copolymer, without SiO2 |
AgeSin® DF-D9901 | Tego Airex 901W | Polyether modified polysiloxane compounds, containing SiO2 |
AgeSin® DF-D9202 | Tego Airex 920 | Modified polysiloxane |
AgeSin® DF-D955R | BYK 055 | Foam-breaking polymer liquid with silicon-free |
AgeSin® DF-T2030 | BYK-1788 | Non-silicone high molecular weight polymer for breaking foam. |
AgeSin® DF-D982V | Tego Airex 900;Tego Foamex N;Shin-Etsu KS66 | Polysiloxane compound with hydrophobic particles |
AgeSin® DF-D980 | Tego Airex 900;Tego Foamex N;ELEMENTIS Defom 6800 | Polysiloxane compound with hydrophobic particles |