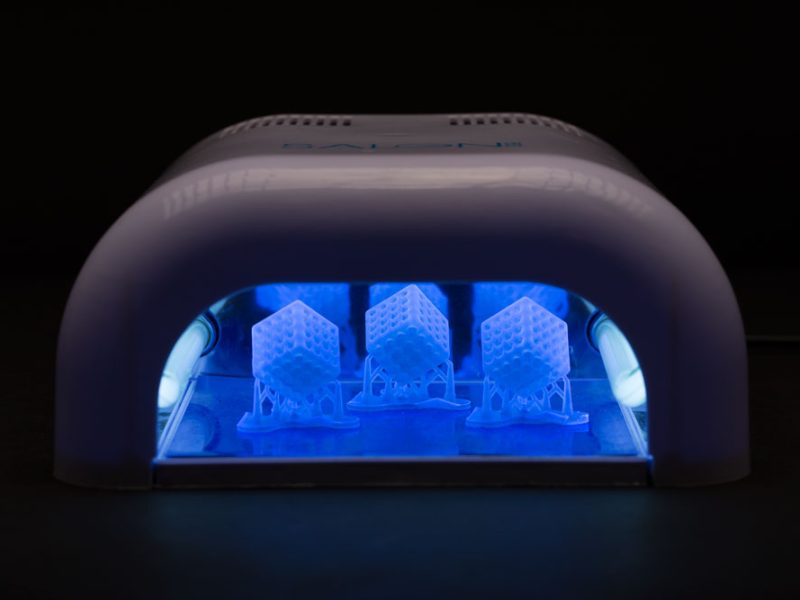
Light-Curing Coatings: Composition, Components, and Applications in Modern Industry
Light-curing coatings have a similar basic composition to ordinary coatings and are composed of the following four types of substances:
General Coatings | Light Curing Coatings |
Resin | Oligomers |
Solvents | Reactive Diluents |
Catalysts | Photoinitiators |
Additives | Various additives |
Light-curing coatings, which are equivalent to ordinary coatings in the resin, are film-forming materials. The performance of the coating plays a significant role in the structure of the oligomer. The oligomer must contain light-curing groups, which are light-sensitive resins.
Light-curing coatings in the active diluent are analogous to ordinary coatings in the solvent. In addition to the dilution effect and the regulation of the viscosity of the system, the active diluent does not volatilize and participates in the light-curing reaction, affecting the rate of light-curing coatings and the mechanical properties of the coating film. The structure of the organic compounds comprises light-curing groups. A photoinitiator is analogous to a catalyst in ordinary coatings. The catalyst employed in ordinary coatings varies depending on the curing method employed, such as oxidation, heat curing, and wet curing. Additionally, light is a crucial factor in the curing process. The curing of coatings is initiated by the absorption of UV light by the photoinitiator, which produces free radicals or cations. These then trigger the polymerization of oligomers and reactive diluent polymerization and cross-linking reactions, leading to the formation of a network structure of the coating film. The additives utilized in these two categories of coatings are largely analogous. They necessitate the incorporation of pigments, fillers, and an assortment of additives. However, light-curing coatings employ additives to mitigate the absorption of ultraviolet light, thereby preventing its interference with the light-curing reaction. Additionally, a specific quantity of light-curing coatings must be combined with a polymerization inhibitor to guarantee the stability of light-curing coatings throughout the manufacturing, storage, transportation, and construction processes.
At present, light-curing coatings represent the largest category of radiation-curing materials in terms of both usage and market share. This chapter provides a comprehensive introduction to the raw materials utilized in light-curing coatings, including photoinitiators, active diluents, oligomers, and additives. The section on photoinitiators introduces the typical hydrogen-capturing radical photoinitiators and cationic photoinitiators, the structure and characteristics of the large molecule photoinitiators developed in recent years, hybrid photoinitiators, water-based photoinitiators, visible-light photoinitiators, and the maleimide-vinyl ether photoinitiator system. It also provides information on the main manufacturers of photoinitiators, products, and applications.
The section on active diluents provides a comprehensive introduction to the structure and characteristics of active diluents, including different functionality active diluents and alkoxylated active diluents, acrylic dioxide, alkoxylated bisphenol A bis (meth)acrylate, vinyl ether active diluents, third-generation (meth)acrylate active diluents, flame retardant phosphorus-containing acrylic esters, a new type of light curing cationic active diluents, and (meth)acrylate with a special functional group. This section will also address the synthesis of commonly used methacrylate active diluents, as well as the manufacturers of these materials. Additionally, it will discuss the methods used to select active diluents, the toxicity of these materials, and the storage and transport requirements associated with them.
The section on oligomers addresses a range of conventional oligomers, including epoxy acrylates, urethane acrylates, polyester acrylates, polyether acrylates, pure acrylic resins, unsaturated polyesters, as well as vinyl resins, organosilicon acrylic resins, epoxy resins, aqueous UV oligomers, hyperbranched oligomers, and double-cured oligomers. The self-initiating functionality of the oligomers, aliphatic and aleo-cyclic synthesis, structure and characteristics of epoxy acrylates, low viscosity oligomers, light-curing polybutadiene oligomers, oligomers for UV-curable powder coatings, and heterogeneous oligomers, as well as the major manufacturers of oligomers, are also discussed. Light-curing coatings are formulated with additives that vary according to their intended application. The section on additives introduces the use of different types of additives in light-curing coatings, including pigments, fillers, additives (defoamers and defoamers, surface control additives, dispersing agents, substrate wetting agents), polymerization blocking agents, extinction agents, thixotropic agents, and so forth.
- The fundamental constituents of light-curing coatings are as follows:
The functionality of light-curing coatings is contingent upon the presence of several key components, which work in concert to achieve the desired properties and performance.
Oligomers are These are film-forming materials in light-curing coatings and are of great consequence in determining the properties of the final coating. Oligomers are required to contain light-curing groups, which renders them light-sensitive resins. The most common types of oligomers are epoxy acrylates, urethane acrylates, polyester acrylates, and polyether acrylates.
Active diluents are These are analogous to solvents in conventional coatings, serving to adjust the viscosity and facilitate application. In contrast to conventional solvents, active diluents do not undergo vaporization; rather, they engage in the curing process, influencing the rate of curing and the mechanical properties of the final film. Examples of such monomers include trimethylolpropane triacrylate (TMPTA) and isobornyl acrylate (IBOA).
Photoinitiators: These are essential for initiating the curing process. Upon exposure to ultraviolet radiation, photoinitiators undergo a chemical decomposition, producing free radicals or cations. These subsequently trigger the polymerization and cross-linking of oligomers and reactive diluents. The most commonly used photoinitiators are benzoin ethers, benzil ketals, and acylphosphine oxides.
Additives: A variety of additives are incorporated with the objective of achieving specific performance characteristics. These include pigments, fillers, defoamers, surfactants, dispersing agents, and thixotropic agents. Additionally, additives are employed to prevent the absorption of UV light, which could otherwise interfere with the curing process. Polymerization inhibitors are also added to ensure stability during the manufacturing, storage, and transportation phases.
- Classification of Photoinitiators
The classification of photoinitiators is based on their mechanism of action.
Radical photoinitiators are defined as: Such photoinitiators generate free radicals upon exposure to ultraviolet radiation. These are further subdivided into Type I (cleavage-type) and Type II (hydrogen abstraction-type) photoinitiators. Examples of this category include benzoin methyl ether and 1-hydroxycyclohexyl phenyl ketone.
Cationic photoinitiators are defined as follows: Upon exposure to ultraviolet radiation, these compounds generate cations, thereby initiating cationic polymerization. One illustrative example is that of diaryliodonium salts.
Hybrid photoinitiators represent a further subdivision of the aforementioned categories. These combine both radical and cationic initiation mechanisms, thereby providing broader curing capabilities and improved properties.
Specialized photoinitiators are a further category of initiators that have been developed for specific applications. The recent emergence of water-based, visible-light, and maleimide-vinyl ether photoinitiators has enabled the development of a new generation of materials, each of which is tailored for specific applications.
- Active Diluents
The selection of active diluents is based on their functionality and impact on the final properties of the coating. The aforementioned categories are defined as follows:
Monofunctional: These provide low viscosity and good flexibility, though they may exhibit limited cross-link density.
Difunctional: These offer a balance between viscosity and cross-link density, and are therefore commonly used in coatings that require a moderate degree of hardness and flexibility.
The tri- and multifunctional categories These compounds enhance the cross-link density of the coating, resulting in a material with high hardness, chemical resistance, and mechanical strength.
Examples of active diluents include:
Alkoxylated bisphenol A bis(meth)acrylate: It offers effective adhesion and chemical resistance.
Vinyl ether active diluents are a type of chemical additive used in the production of coatings. These materials are renowned for their rapid curing rates and exceptional flexibility.
Flame retardant phosphorus-containing acrylic esters These materials are employed in applications that necessitate flame retardancy.
- Oligomers are of paramount importance with regard to the functionality of light-curing coatings. These oligomers are responsible for determining the properties of the material, including flexibility, hardness, chemical resistance, and adhesion. The principal categories of oligomers are as follows:
Epoxy Acrylates: These oligomers offer excellent adhesion, chemical resistance, and mechanical properties.
Urethane acrylates are These materials are renowned for their flexibility, toughness, and resistance to abrasion.
Polyester acrylates are a type of acrylic polymer that is composed of repeating units of carbonate and ester groups. They provide an optimal balance of flexibility and hardness.
Polyether acrylates are a category of acrylic polymers that feature ether linkages in their chemical structure. These materials are typically employed due to their low viscosity and favorable elongation properties.
Notable recent advancements include the development of hyperbranched oligomers and self-initiating oligomers, which offer enhanced curing efficiency and performance.
- Additives
The function of additives in light-curing coatings is to enhance performance and application properties.
Pigments and fillers are used in the manufacture of coatings to impart specific properties to the finished product. They provide color, opacity, and mechanical strength.
Defoamers: The objective is to prevent foam formation during the application process.
Surfactants and dispersing agents are also employed in the formulation of light-curing coatings. They facilitate the dispersion of pigments and enhance the wettability of the material.
Polymerization inhibitors are chemical compounds that impede the polymerization process. It is imperative to guarantee the stability of the formulation during the storage period.
Thixotropic agents are substances that can be used to modify the rheology of a substance, preventing it from sagging and improving its application properties. Modification of the rheological properties may be employed to prevent sagging and to enhance the quality of the application.
- Applications and Market Trends
Light-curing coatings are employed extensively across a range of industries due to their rapid curing times, minimal environmental impact, and superior performance characteristics. Key applications include:
Automotive: Clear coats, primer surfacers, and repair coatings.
Electronics: Conformal coatings