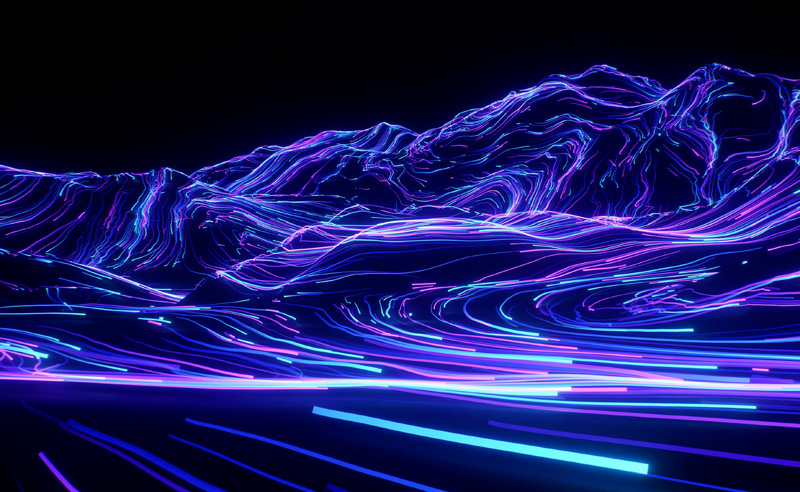
Light-Curing Coatings in Wood Industry: Applications, Types, and Formulation Insights
Light-curing coatings are used in many fields because of their advantages of fast drying and curing, environmental protection and energy saving. Early light-curing coatings are mainly used in wood coating, nearly two decades, with the success of efficient photoinitiators, active diluents and oligomers continue to research and development, and to see the market, UV curing applications to be gradually expanded, of which the largest amount of supply and demand for light-curing coatings, light-curing coatings can be divided into the application areas of light-curing bamboo coatings, light-curing paper coatings, light-curing plastic coatings, light-curing Vacuum coating coatings, light-curing metal coatings, light-curing fiber optic coatings, light-curing conformal coatings, light-curing glass, ceramics, stone coatings, optical disc protective coatings, light-curing leather coatings, light-curing automotive coatings, light-curing aqueous coatings, light-curing powder coatings, light-curing antistatic coatings, light-curing flame retardant coatings, cationic light-curing coatings, light-curing fluorocarbon coatings, and electron-beam light-curing coatings and so on. At present, light-curing bamboo coatings and light-curing plastic coatings are the largest applications. With the continuous development and progress of light-curing technology, light-curing coatings have been rapidly developed, the applicable substrates have been expanded from bamboo, paper, plastic to metal, stone, cement products, fabrics, leather, glass and so on. Light-curing coatings can also be applied to a variety of industrial fields, including bamboo wood flooring, decorative panels, furniture, plastic panels, printing cans of paint, plastics, metal parts, electronic components, paper and other industrial coatings, parts, car body, safety glass and other automotive coatings, as well as fabrics, printing and dyeing and other decorative coatings. The appearance of light-curing coatings from the initial high-gloss type, the development of matte type, frosted type (imitation metal etching), metal flash type, pearlescent type, hot stamping type, texture type. Diversification of coating methods, including roller coating, scraping, coating, spraying, dip coating, electrostatic spraying, and so on.
Light-curing bamboo wood coating is a light-curing coating products in a larger production of a class, but also the earliest industrialisation of light-curing coatings. the early 1960s, the German Bayer company successfully researched the first generation of light-curing coatings, namely, light-curing bamboo wood coatings. The characteristics of light-curing bamboo wood coatings lie in the excellent coating properties, fast curing, product stability in the application of equipment, low processing costs, low or zero organic volatile matter emissions. The application of light-cured coatings on bamboo wood products consists of three main aspects, i.e. dip-coating (plasticised wood alloy), filling (sealing and putty) and overprinting. According to the use of occasions and quality requirements, light-curing bamboo wood coatings can be divided into wood parquet coatings and decorative panel coatings, but also can be divided into varnish and colour coatings. The majority of coating methods are mainly roller coating, but also some spraying, drenching, scraping and so on. In terms of construction function, light-curing bamboo wood coating includes UV putty paint, UV primer and UV top coat.
1.UV putty paint for bamboo wood
UV putty paint is usually used for wood with poor surface smoothness, such as chipboard, fibreboard, etc. Its function is to fill the small holes and micro defects of the substrate, seal the surface of the substrate, so that the decorative coatings subsequently applied will not be sucked in and cause the appearance of unevenness, thus providing a smooth surface for coarse materials. UV putty paint is usually a paste, which contains a high proportion of inorganic fillers in addition to photoinitiators, oligomers, active diluents and other basic components of light-curing coatings. Selection of fillers should be considered on the curing rate of low impact that is, low refractive index and easy to sand, filler with good performance. Choose the right filler can improve the coating hardness, impact resistance, reduce curing shrinkage, improve adhesion.UV putty paint used in the inorganic filler, including talcum powder, heavy and light calcium carbonate, barite powder, dolomite powder. Unsaturated polyester system UV putty paint cheap, acrylic system resins and monomer application to accelerate the curing rate and coating thin and full-bodied appearance.
UV primer and UV putty paint and the use of different occasions and role, UV putty paint is commonly used in the surface of flat, poor smoothness of the wood, while the UV primer is applied to the surface of the wood is relatively smooth and flat. UV primer and UV putty paint contains less inorganic filler compared to the viscosity is lower, close to the viscosity of the UV topcoat. After coating a layer of UV primer, low viscosity paint can penetrate to the wood small openings, through the refraction effect of the film layer to retain and strengthen the natural beauty of the wood grain and pore structure, UV light curing, sandpaper mechanical sanding, and then UV topcoat masking curing, to get flat, smooth, full of masking effect. UV primer added inorganic filler and UV putty paint to add filler in the same varieties and the same role. Coated UV primer and UV putty paint surface need to be sanded, the purpose of sanding is to enhance the UV topcoat and UV primer or UV putty paint between the layers of adhesion to prevent the topcoat off. In addition, UV primer sometimes add a small amount of zinc stearate, which can play a lubricating effect, when sanding the surface of the coating can also prevent too much “white fog”. It should be noted that many metal salts of stearic acid (such as zinc stearate, aluminium stearate, etc.) can produce a weak matte effect, so the choice of inorganic filler should be considered when the refractive index of the filler, refractive index of the filler in the UV incident wet film occurs many times refraction and reflection, preventing the light from penetrating directly into the film, affecting the curing performance.
UV top coat and UV putty paint and UV primer in the composition of the main difference is that the former does not contain inorganic fillers, if you want to get matte or frosted effect, you can also add appropriate silica powder matting agent.UV top coat is widely used in natural wood or wood finishes, to produce high-gloss closed grain finishing effect. A variety of acrylic coatings can be formulated according to different applications, including high gloss and matte coatings, coloured and colourless coatings, roll, drench and spray coatings, furniture, hardwood flooring or cork board coatings, and so on. In general, it is difficult to formulate UV topcoats with a completely matt finish, and SiO2 with a particle size of 25 μm is often chosen as a more suitable matting agent. It is also possible to use a combination of processing techniques to adjust the gloss level, one method is to use a combination of electron beam curing and UV light curing, so that the surface of the coating produces very fine wrinkles to achieve the effect of low gloss; another method is to use a different type of UV light source for double curing, first irradiated with a low-pressure UV lamp, and then with a high-pressure mercury lamp for secondary curing, which achieves the effect of the surface of the low-gloss.