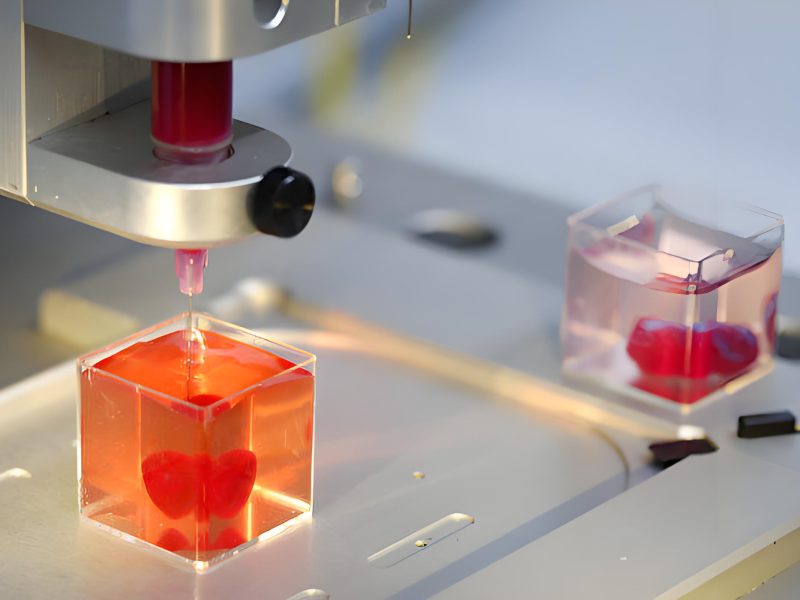
Application of 4D printing in biomedical field
Regenerative medicine is a branch of medicine that includes tissue engineering, therapeutic stem cells and artificial organs. Among them, tissue engineering can produce artificial tissues for repairing damaged or diseased tissues. When constructing complex polymer structures of non-biological scaffolds and cells, the most effective method is 3D printing technology, which can transform pre-built digital blueprints into objects by printing layer by layer.
In daily life, we often use printers to print various documents and materials. This printing is usually done on a plane, which can be called 2D printing. Subsequently, researchers developed 3D printing technology, which directly uses 3D printers to print with a variety of powdered, liquid or molten materials as inks to directly print macroscopic three-dimensional 3D structures, such as houses, bones, cars, food, parts and other three-dimensional structures.
However, the current 3D printing technology has many limitations, such as the inability to take into account the resolution of the printed body, biocompatibility, cell activity and mechanical properties. 4D bioprinting technology can be widely used in fields such as regenerative medicine, materials science, chemistry and computer science, and is becoming the next generation of bioprinting technology.
Introduction to 4D printing technology
4D printing technology was originally defined as “3D printing technology + time”. It adds the fourth dimension – time – on the basis of 3D printing. That is, under the stimulation of external conditions (mainly heat, magnetism, light, humidity, pH, etc.), the printed product will change the shape, properties or functions we need over time, thus giving 3D printed products vitality. This is where 4D printing technology is more advanced than 3D printing technology, which can make artificial tissues environmentally responsive.
People can set the model and time through software, and the deformable material will deform into the required shape within the set time. To be precise, 4D printing is a material that can deform automatically. The design is directly built into the material. It can automatically fold into the corresponding shape according to the product design without connecting any complex electromechanical equipment.
The key to 4D printing is memory alloy. 4D printing was developed by the Massachusetts Institute of Technology (MIT) and the Stratasys Education Research and Development Department. It is a revolutionary new technology that allows materials to be quickly formed without a printing machine, and the size and shape can change over time.
There are three mysteries behind 4D printing: precise machines, composite materials, and smart programs.
The logic of 4D printing is to embed product design into deformable smart materials through printers. Under specific time or external stimulation conditions, it can self-assemble according to the pre-designed design without human intervention or power supply. Compared with 3D printing, 4D printing is more intelligent. Materials can be “created” by themselves, which simplifies the printing process, but has higher requirements for printing materials.
4D printing smart materials
Smart materials generally refer to materials that respond to environmental changes under specific conditions, have the ability to self-perceive, self-diagnose, self-drive, and self-repair, and have multifunctionality and the ability to sense environmental changes. Shape memory alloys, shape memory polymers, piezoelectric materials, electroactive polymers, light-driven polymers, etc. are all smart materials.
01
Temperature-driven materials
1) Shape memory alloy: Shape memory alloy refers to an alloy material that can completely eliminate its deformation at a lower temperature and restore its original shape before deformation after heating, that is, an alloy with a “memory” effect.
The structure and mechanical properties of shape memory alloys are extremely sensitive to temperature changes. They have a strong affinity for N, O, and H at high temperatures. They easily absorb these gases during the molding process and form brittle compounds at the molding interface. In order to maintain the shape memory effect during the molding process, martensitic phase transformation should be prevented, and the size of the heat-affected zone should be controlled to prevent grain growth from destroying the ordered lattice structure of the parent material and affecting its shape memory effect.
2) Shape memory polymer: Shape memory polymer (SMP) is a new type of functional polymer material. According to the different shape memory mechanisms, it can be divided into two categories: solid shape memory polymer materials and polymer gel systems; according to the different conditions for realizing the memory function, it can be divided into thermosensitive, photosensitive, and solvent-sensitive types.
At present, most commonly used shape memory polymers are thermosensitive shape memory polymer materials. Their shape memory effect originates from the glass transition or melting transition of the molecular chain components, while the shape memory effect of shape memory alloys is caused by the reversible martensite/austenite transformation of the alloy lattice. Compared with shape memory alloys, shape memory polymers are easier to form.
02
Electrically driven smart materials
1) Piezoelectric crystal materials: Piezoelectric crystals refer to materials with piezoelectric effect. The additive manufacturing of piezoelectric materials using inkjet printing can realize the manufacturing of complex microstructures, which is difficult to achieve with traditional processing methods. By doping and surface treating the printed materials, the performance of piezoelectric materials can be improved, so that they can be used in the fields of bioengineering and sensors.
2) Dielectric elastic material (DE): DE is a type of electroactive polymer (EAP). It can produce large deformation under the action of an external electric field. When the external electric field is removed, it returns to its original shape or volume. Therefore, it can be designed and manufactured into intelligent conversion devices, such as drivers, sensors and energy harvesters.
Silicone rubber and acrylic acid are the two most common dielectric elastic materials, and the additive manufacturing process of DE materials generally uses two-component silicone rubber as the precursor material. The ultimate goal of printing is the curing of the two-component material.
3) Ionic polymer metal composite (IPMC): IPMC is another electroactive polymer that can achieve large deformation at low voltage (0.5~10V). It is a composite material with a sandwich structure formed by depositing and infiltrating a layer of metal electrodes on the surface of a substrate membrane (usually an ion exchange membrane) by physical or chemical methods.
4) Buck gel material: Buck gel is a newly developed ionic electroactive polymer structure. Its structure also consists of 3 layers, but the intermediate matrix material is an electrolyte composed of polymers and ionic liquids, and the two sides are electrode materials composed of carbon nanotubes, polymers, and ionic liquids.
03
Water-driven smart materials
In addition to being realized through the additive manufacturing method of smart materials, 4D printing can actually be realized by printing out deformable smart structures. Water-driven smart structures are a typical example. Water-driven smart structures are mainly designed based on the water absorption characteristics of the material, and ultimately the structure evolves into a pre-set shape.
04 Light-driven smart materials
The three components of photosensitive materials (SINOMER PETMP, MDTVE and SINOMER EGDMP) were mixed in a mass ratio of 1:5:4 to form a mixed liquid for manufacturing light-driven smart materials. 1% of the mass of the mixed liquid was added with photoinitiators SINOCURE 184 and SINOCURE 819. A light-sensitive film was prepared under light of 400-500 nm and a power of 40mw/cm2. NOA65 photocurable adhesive was cured as a core layer structure to form a sandwich composite structure with the light-sensitive film. The experiment found that the light-driven composite structure underwent obvious bending deformation under light, and the bending deformation was closely related to the thickness ratio of the light-sensitive film layer to the NOA65 layer and the elastic modulus ratio.
The obvious advantage of light-driven materials is that single-point remote drive control can be achieved through light, and light is a wide source of driving power, and the response speed is comparable to that of shape memory polymers.
05
Magnetic drive materials
Using the direct writing (DW) method, a shape memory polymer solution is prepared and mixed with Fe304, benzophenone, and photosensitizer to print a spiral structure with temperature and magnetic drive. The key to printing this drive material is to add magnetic substances to the printing solution, which is currently less studied.
06
Hydrogel materials
The hydrophilic poly (N-isopropylacrylamide) (NIPAM) and hydroxyethyl methacrylate (SINOMER HEMA) are mixed and printed. The resulting structure can achieve folding and flattening under the drive of temperature and humidity.
The printing of hydrogel materials is currently studied more, but the deformation is mostly based on the swelling principle. The main form of drive for this type of material is water drive, and the printed structure is highly dependent on the environment.
Application of 4D printing in biomedical field
4D printing is a comprehensive technology based on deformable materials and 3D printing technology. Among deformable materials, shape memory polymers (SMP) are the most widely used.
Application and potential applications of 4D printed shape memory polymers in biomedical field
SMP has the characteristics of light weight, strong recovery performance, mild recovery conditions, biodegradability, low biological toxicity or even non-toxicity. A variety of excellent properties make its application in biomedical field particularly prominent, such as SMP sutures, SMP dental braces, SMP aneurysm occluders, etc., but the structures of these SMPs are almost all simple linear structures, similar to the relatively complex, personalized and high-precision structures such as heart stents, bone stents, and tracheal stents. Traditional preparation technology is difficult to achieve, and the emergence of 4D printing makes up for this deficiency.
01
Tracheal stent
Morrison et al. used SLA 3D printing technology to prepare a tracheal stent with polycaprolactone (PCL) as the printing material, and successfully applied it to the treatment of severe tracheobronchomalacia. According to the patient’s CT scan image and medical digital imaging technology, a 3D tracheal model was constructed, a three-dimensional graphic in STL format was designed, and the trachea and stent model were simulated and combined on the computer. It was implanted into the patient’s body through surgery and cured 3 patients.
Postoperative in vivo tests showed that the tracheal stent can be biodegraded by the human body as the patient grows. After 3 years, when the patient’s trachea grows well, the material can also be biodegraded by the human body, eliminating the pain of multiple surgeries for the patient. Based on this, a tracheal stent with shape memory effect prepared by 3D printing SMP material came into being.
02
Cell scaffold
The cell scaffold prepared by 4D printing SMP can induce cell proliferation and differentiation. Miao et al. started with materials and synthesized a new type of renewable soybean oil epoxidized acrylate material, which enhanced cell adhesion and proliferation compared with traditional PEGDA; Hendrikson et al. started with changing the fiber arrangement direction of the scaffold and prepared two types of cell scaffolds with fiber arrangement directions, confirming that the mechanical stimulation of the cell scaffold deformation on the cells can lead to the directional growth of cells and cell nuclei; Miao et al. started with the internal structure of the scaffold and prepared a scaffold with a biomimetic gradient void structure, where cells can grow inward along the voids, and the voids can also play a role in transporting nutrients and metabolic waste. These three research examples developed and tested some excellent properties of 4D printed SMP cell scaffolds from different angles. At present, there are still few types of SMP suitable for 4D printing and with high biocompatibility. The research and development of 4D printing technology and highly biocompatible smart biomaterials will guide the design and development of new functional biomedical scaffolds in the future.
03
Vascular stent
Wei et al. from Harbin Institute of Technology added magnetic Fe3O4 nanoparticles as functional particles to polylactic acid (PLA) to prepare a shape memory composite material that can be deformed by magnetic drive. Experiments show that the spiral stent structure based on this material can be autonomously unfolded under the action of a magnetic field, and the entire unfolding process can be completed within 10 seconds.
Self-expanding vascular stents can be used to treat cardiovascular diseases such as vascular stenosis caused by thrombosis. When the self-expanding vascular stent reaches the narrow part of the blood vessel, the stent is unfolded by adjusting the strength of the external magnetic field, and the diameter of the vascular stent becomes larger, thereby supporting the narrow blood vessel and allowing blood to circulate normally.
This technology not only realizes the intelligent remote control of medical devices, but also provides new possibilities for minimally invasive surgery. It has great application prospects in the intelligentization and personalized customization of human implants, and is also of great significance to the further development of the biomedical field.
04
Bone scaffold
Senatov et al. mixed polylactic acid (PLA) and hydroxyapatite (HA) in a mass ratio of 20:3, and used FDM to print a porous scaffold with shape memory function for bone defects.
The porous PLA/HA scaffold has excellent adhesion to MSCs, supporting cell survival and stimulating cell proliferation, which is a key prerequisite for its medical application; the presence of MSCs in the scaffold is conducive to the formation of blood vessels at the implantation site. This shape memory scaffold that can support the growth and proliferation of MSCs has great prospects in the application of adaptive implants for bone replacement.
05
Heart scaffold
Cabrera et al. combined FDM with medical technology to prepare a scaffold that can be used in in vivo heart valve remodeling surgery. This scaffold has a mesh structure that can be reduced to a certain extent and expands after implantation to automatically restore to its original shape, which is suitable for pediatric patients.
Mechanical property tests show that its mechanical properties are comparable to those of conventional nickel-titanium alloy scaffolds used for heart valve implantation in animal experiments; in vitro degradation characterization experiments prove that the scaffold can also be biodegraded. The use of 4D printing technology to prepare a mesh-structured shape memory heart stent has broad application prospects in the biomedical field.
06
Other applications
1) Yang et al. used improved FDM to perform 4D printing with polylactic acid (PLA) or polyether ketone (PEEK) and continuous carbon fiber (CF) as printing materials, and manufactured two (CF/PLA and CF/PEEK) intelligent structural parts that can be directly or indirectly activated by temperature to achieve deformation effects. This 4D printed intelligent composite material that can be driven by heat or electricity to produce shape changes can be used in the manufacture of bionic sensors and artificial muscles.
2) Researchers at the Massachusetts Institute of Technology used 4D printing technology to manufacture a micro drug capsule, which was driven by temperature to cause the capsule to undergo corresponding shape changes. When the body temperature is too high due to fever symptoms caused by certain diseases, the capsule will deform and the drug in it will be released. The timing of drug release is further controlled by body temperature. When humans are not sensitive to the rise in body temperature, the drug is released at the first time, which is impossible for traditional drugs.
3) The Xijing Hospital of the Fourth Military Medical University has developed a biodegradable material. Based on this material, a biodegradable prosthesis was printed using 4D printing technology, which was successfully implanted into the patient for breast reconstruction. Long-term follow-up examinations after surgery found that the prosthesis had good tissue compatibility, autologous fibrovascular tissue began to grow and gradually grew into the prosthesis. The prosthesis could be completely degraded by the human body within the next two years, and the autologous fibrous tissue would eventually completely replace the prosthesis. This 4D printed SMP prosthesis not only avoids residue in the body, but also ensures the appearance of the breast and improves the quality of life of patients.
The application of 4D printed SMP in the field of biomedicine has broken the technical bottleneck of traditional medical devices, bringing more possibilities for clinical minimally invasive surgery, reducing the number of surgeries, controlled drug release, tissue and organ replacement, etc., and 4D printed SMP can quickly and accurately provide medical services based on the patient’s personal situation, provide patients with personalized treatment plans, reduce patient pain, and improve the quality of life.
4D printed SMP provides a new development direction for the further development of biomedicine. As more and more new shape memory materials that can be used for bioprinting are successfully developed and 4D printers are continuously developed, more personalized smart medical devices will be used in the future biomedical field. The organic combination of 4D printing SMP and the biomedical field is a new trend in the development of the medical field in the future.