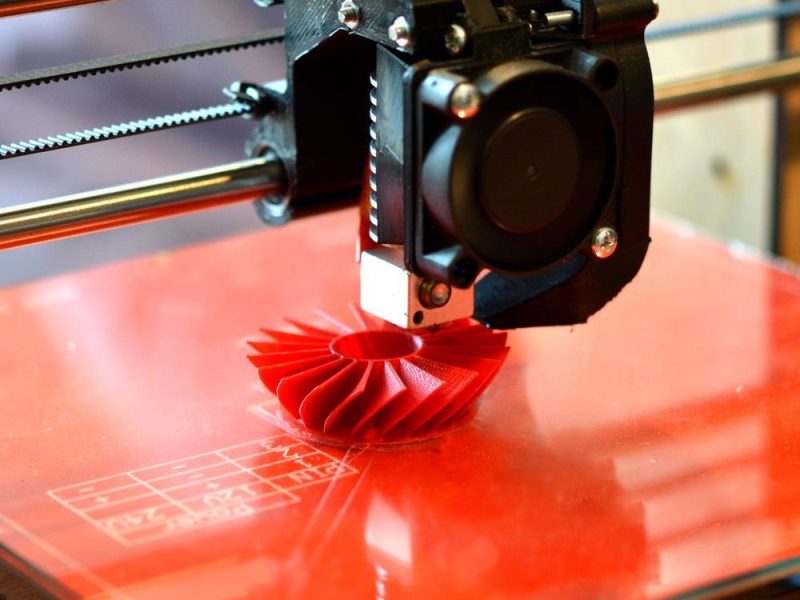
Advancements in 3D Printing Technologies: Aluminum Alloy Applications, Light Curing Methods, and SLS vs SLA Comparison
1.What are the application areas of aluminum alloy 3D printing?
- Aerospace field
The application of aluminum alloy 3D printing in the aerospace field is extremely important, mainly reflected in the following aspects:
Complex structure manufacturing: Aluminum alloy 3D printing technology can manufacture aviation parts with complex structure, such as engine mounts, fuel injectors, etc., which are difficult or costly to realize under traditional manufacturing methods.
Lightweight design: The combination of the lightweight and high-strength characteristics of aluminum alloys and the flexibility of 3D printing can optimize structural design and material distribution to achieve weight reduction in aerospace vehicles, thereby improving flight efficiency, reducing fuel consumption and reducing environmental impact.
Performance enhancement: Through precise control of printing parameters and heat treatment and other post-treatment processes, the mechanical properties and corrosion resistance of aluminum alloy parts can be enhanced to meet the demand for high-performance materials in the aerospace field.
- Automobile manufacturing field
In the field of automobile manufacturing, aluminum alloy 3D printing technology also shows great potential:
Lightweight design: Aluminum alloy 3D printing technology can be used to manufacture key components such as automotive engine blocks, cylinder heads, chassis parts, etc. By optimizing material distribution and structural design, it can realize lightweighting of the entire automobile and improve fuel economy and driving safety.
Rapid prototyping: Compared with traditional manufacturing methods, aluminum alloy 3D printing can greatly shorten the product development cycle, rapidly iterate the design, and provide faster market responsiveness for automakers.
Customized production: With the increase of consumers’ demand for personalized automobiles, aluminum alloy 3D printing technology can realize small-lot, customized production to meet the diversified needs of the market.
- Medical device field
In the field of medical devices, aluminum alloy 3D printing technology also plays an important role:
Personalized customization: Aluminum alloy 3D printing technology can be used to manufacture personalized customized orthopedic implants, dental restorations and other medical devices to meet the specific treatment needs of patients.
High-precision manufacturing: medical devices require high precision and performance, aluminum alloy 3D printing technology can achieve high-precision manufacturing to ensure the quality and safety of medical devices.
- Other Fields
In addition to the above fields, aluminum alloy 3D printing technology can also be applied to electronic products, industrial machinery, art creation and many other fields. Through customized design and rapid printing, aluminum alloy 3D printing technology can better meet the needs of different industries and promote product innovation and upgrading.
- Advantages and Challenges
Advantage:
Increased design freedom: 3D printing technology can realize the manufacture of complex structures, breaking the limitations on design imposed by traditional manufacturing processes.
High material utilization: compared with traditional subtractive manufacturing methods, 3D printing adds materials on demand, reducing material waste.
Rapid prototyping and small batch production: shorten the product development cycle, reduce cost and threshold.
Challenges:
High cost: the current investment and material cost of aluminum alloy 3D printing equipment is relatively high.
Relatively low printing efficiency: need to further improve the printing speed to meet the needs of mass production.
Insufficient standardization of materials and processes: a unified standard and certification system needs to be developed to ensure the quality and performance of parts.
2.Light Curing: What is SLA, DLP and LCD?
- SLA (Stereo Lithography Appearance) is sometimes abbreviated to SL. Like other light-curing technologies, layer-by-layer printing forms 3D solids.
SLA uses an ultraviolet laser as the light source, and the laser spot is precisely controlled by a rotating mirror to scan the cross-section profile, curing one layer and then the next, so that the layers are stacked up to form a three-dimensional entity.
The main advantages of this method are greater precision and better print quality, as the precise movement and tiny dimensions of the laser allow for better detail and resolution. This improved quality comes at the cost of print speed, so plotting each layer can be more time-consuming.
- DLP (Digital Light Processing) uses a UV projector as a light source and works by controlling the light projected through a digital micromirror primary (DMD). One layer is projected at a time, curing an entire layer at a time. Therefore, in terms of speed, DLP is faster compared to SLA.
The printing accuracy of DLP decreases as the projected area increases, so the print size is limited by the resolution of the projector.
- LCD (Liquid-crystal display) printing is a new technology that has only emerged in the last few years, and is sometimes referred to as DUP (Direct UV Printing).
All LCD 3D printers work on the same core principle: they illuminate a cross-section of a 3D print by using an LCD screen to mask the UV light source. Essentially, this replaces the DLP projector unit with a more compact, cheaper screen, but at the cost of print resolution and printer durability. So, as time passes, the LCD screen may wear out, while the DLP projector will last longer. The latest black and white LCD screens now have a theoretical life of over 2,000 hours, a significant improvement over previous color screens (which were basically less than 500 hours).
With LCD printing, you can get DLP equivalent speed, and the equipment is lighter, smaller and cheaper.
3.Which is better, SLS nylon 3D printing or SLA light-curing 3D printing?
- SLS Nylon 3D Printing
Advantage:
Material Versatility: SLS technology allows for the use of a wide range of materials, especially nylon, which has excellent mechanical properties and durability, making it suitable for functional testing, rapid prototyping, and application scenarios that require resistance to high temperatures and chemical corrosion.
No support structure required: During SLS printing, the unsintered powder naturally supports the overhang without the need for additional support structures, which improves material utilization and reduces costs.
High molding efficiency: SLS technology enables stacked printing of models in the molding cylinder, which effectively improves molding efficiency and is suitable for direct production of small and medium-lot products.
High molding accuracy: by adjusting the printing process parameters, SLS technology can control the printing error of the model to about ±0.1-0.2%mm.
Disadvantage:
Surface roughness: compared to SLA technology, the surface finish of SLS printing is usually poorer and may require subsequent processing.
Higher equipment costs: SLS printers are more expensive and post-processing (e.g. sandblasting, etc.) requires additional costs.
Material Shrinkage: Nylon and other powdered materials will shrink after sintering, which needs to be taken into account when designing the model.
- SLA Light Curing 3D Printing
Advantage:
High precision: SLA technology is ideal for printing objects with complex structures and fine dimensions.
Good surface quality: SLA-printed parts have a smooth surface and a quality close to that of injection-molded parts, making them suitable for applications that require a high surface finish.
Fast molding speeds: While slower when printing large size models, SLA technology is relatively fast for molding small size parts.
Material selection: although SLA primarily uses liquid photosensitive resins, there is a wide variety of such materials with different mechanical properties and characteristics.
Disadvantages:
Need for support structures: SLA usually requires the design of support structures when printing complex shapes, which increases the complexity of subsequent processing.
High material costs: Liquid photosensitive resins are more expensive, which increases printing costs.
High equipment cost: SLA systems require sophisticated equipment to manipulate the liquid, which is expensive to build and maintain.
Comprehensive Comparison
Accuracy and Surface Quality: If the project requires a high degree of accuracy and surface quality, SLA technology may be a better choice.
Cost and Efficiency: For projects requiring rapid prototyping or small to medium volume production with some consideration for cost, SLS technology may be more advantageous.
Material Selection: It is also important to select the right material for the specific application. SLS technology offers a wider range of material choices, especially engineering grade materials such as nylon, while SLA technology focuses on liquid photosensitive resins.