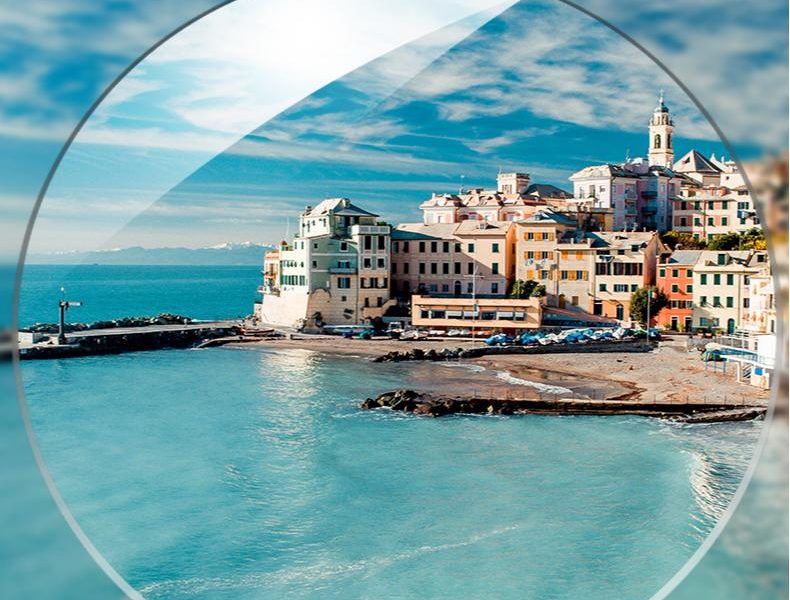
Evolution of resin lens materials
Spectacle lens materials have evolved from several generations of materials, such as optical glass, CR-39, PC/acrylic, and polyurethane resin. From the 1960s to the 1980s, resin lenses quickly surpassed glass as the main material for spectacle lenses. As the refractive index of the lens increases, its dispersion phenomenon will increase and the Abbe number of the lens will decrease. Therefore, from the development history of resin lenses, its material has been improved mainly along the path of increasing the refractive index and taking into account the Abbe number.
- First generation: CR-39 (low refractive index lens)
Allyl diglycol dicarbonate, which is the common CR-39 material now, was originally developed by PPG in the United States in the 1940s and gradually applied to eyeglass lens materials, improving the fragility of glass materials. CR-39 lenses have a high Abbe number, excellent optical performance, and a refractive index of 1.49. They have become the most widely used material in low refractive index lenses. Usually, at the same degree, the lower the refractive index of the lens, the thicker the lens. The CR-39 lens with a refractive index of only 1.49 will inevitably cause consumers to wear heavy problems, so seeking higher refractive index lens materials has become the focus of subsequent research.
- Second generation: Acrylic, PC (medium and high refractive index lenses)
In the 1970s and 1980s, acrylic and PC were gradually used as eyeglass lens materials with a refractive index between 1.56 and 1.60. The second generation of resin lens materials was thus opened and became the representative material of medium refractive index lenses. PC material has low specific gravity and strong impact resistance, but its Abbe number is low, only about 29. Acrylic (PMMA, polymethyl methacrylate) is used as a material for eyeglass lenses. It is low-cost and easy to process, but its Abbe number is low and its impact resistance is poor.
- Third generation: polyurethane material (high refractive index lens)
In 1987, Mitsui Chemicals first applied polyurethane material to eyeglass lenses and named it “MR” lens material, opening the era of high refractive index lenses, that is, the third generation of resin lens materials. At present, Mitsui Chemicals has launched polythiourethane lens materials such as MR-8, MR-7/10, and MR-174, with a refractive index range of 1.60 to 1.74, meeting the different wearing needs of consumers. Compared with traditional resin lens materials, this type of lens material has the advantages of high refractive index, low dispersion, light weight, wear resistance and impact resistance. At the same time, while maintaining high light transmittance, the material’s haze index, UV blocking ability and other properties have also been improved. It has now become the industry’s preferred material for high refractive index eyeglass lenses.
Production process of polythiourethane lenses
Polythiourethane lenses have extremely high requirements for the purity, chromaticity, refractive index and other indicators of monomer materials. At present, the production of this lens material adopts a one-time thermal curing molding process, which can be divided into two process steps: prepolymer production and polymerization curing. In the prepolymer production stage, the basic chemical raw materials are mixed according to a certain formula ratio, supplemented by a catalyst, a specific temperature, and an environment, and a large molecular prepolymer is generated after a certain period of polymerization reaction. In the lens curing stage, the prepolymer is injected into the lens mold, and under a specific temperature and environment, it is polymerized and cured for a certain period of time to form a solid lens substrate.
1.60 High Refractive Index Polyurethane Lens Operating Instructions:
- 1kg Grade Ingredients
Ingredient | Ingredient ratio | Additional amount(g) | Remarks |
A(HXDI) | 49.5% | 495 | |
SINOMER BMPT | 30% | 300 | |
SINOMER PETMP | 20.5% | 205 | |
Initiator(SIPEROX DCP) | 0.08% | 0.8 | |
SINOSORB UV-329 | 1-1.5% | 10-15 |
Add according to your needs |
SINOSORB UV-326 | 0.3-0.5% | 3-5 | |
Release agent | 0. 1% | 1 | |
Colorant | 0.05% | 0.5 | Add according to your needs |
- Operation procedures
1) Preparation
① Vacuum conditions: <2torr;
② Indoor conditions: humidity 45%-55%;
2) Batching steps
① At room temperature, mix A and all auxiliary components in a mixing bucket according to the proportion, stir until completely dissolved, and obtain material I;
② Add SINOMER BMPT and SINOMER PETMP components according to the proportion, maintain the material temperature at 12℃, and stir and degas for 70 minutes;
③ Stop stirring and degas for 20 minutes;
④ Fill.
3.Primary curing procedure
Temperature | State | Time |
25℃-25℃ | Maintain | 3h |
25℃-45℃ | Heat up | 3h |
45℃-50℃ | Heat up | 2h |
50℃-60℃ | Heat up | 3h |
60℃-120℃ | Heat up | 5h |
120℃-120℃ | Maintain | 3h |
120℃-70℃ | Cool down | 2h |
4.Secondary curing procedure
Temperature | State | Time |
70℃-120℃ | Heat up | 1h |
120℃-120℃ | Maintain | 2h |
120℃-70℃ | Cool down | 1h |
- 1.67 High Refractive Index Polyurethane Lens Operating Instructions:
- 1kg Grade Ingredients
Ingredient | Ingredient ratio | Additional amount(g) | Remarks |
A(XDI) | 52.0% | 520 | |
B(SINOMER BMPT) | 48.0% | 480 | |
Initiator(SIPEROX DCP) | 0.012% | 0.12 | |
SINOSORB UV-329 | 0.8%-1.5% | 8-15 |
Add according to your needs |
SINOSORB UV-326 | 0.3%-0.5% | 3-5 | |
Release agent | 0.08% | 0.8 | |
Colorant(Blue) | 0.02%-0.2% | 0.2-2 | Add according to your needs |
Operation procedures
1) Preparation
① Vacuum conditions: <2torr;
② Indoor conditions: humidity is recommended to be <50%;
2) Batching steps
① Add component B to the mixing tank in proportion and cool with circulating water at 8℃~10℃;
② At room temperature, mix component A, UV powder, toner, and release agent in a mixing barrel in proportion and stir until the solid is completely dissolved to obtain material I; use 1 kg of A to dissolve the initiator alone to obtain material II;
③ Transfer material I to the mixing tank and stir rapidly for 60 minutes; then add material II and stir rapidly for 20 minutes; reduce the stirring speed to about 1r/s, cool with circulating water at 8℃~10℃, and slowly stir to degas for 10 minutes;
④ Stop stirring, cool and keep warm with circulating water at 8~10℃, and fill.
3.Primary curing heating scheme
Temperature | State | Time |
30℃-30℃ | Maintain | 3h |
30℃-45℃ | Heat up | 3h |
45℃-50℃ | Heat up | 1.5h |
50℃-60℃ | Heat up | 2h |
60℃-120℃ | Heat up | 4h |
120℃-120℃ | Maintain | 4h |
120℃-70℃ | Cool down | 2.5h |
70℃-70℃ | Maintain | 2h |
4.Secondary curing heating scheme
Temperature | State | Time |
70℃-120℃ | Heat up | 1h |
120℃-120℃ | Maintain | 3h |
120℃-70℃ | Cool down | 1h |