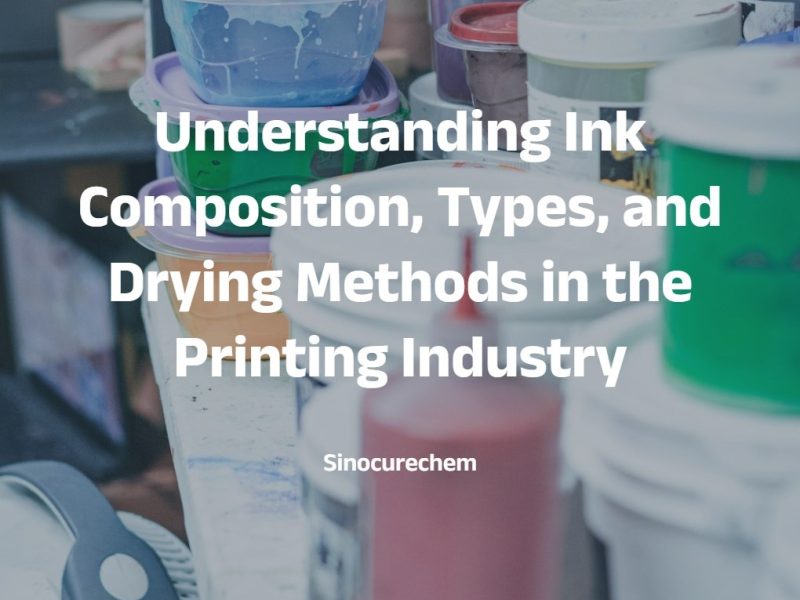
Understanding Ink Composition, Types, and Drying Methods in the Printing Industry
Ink is a homogeneous mixture of connecting materials, colored bodies (pigments, dyes, etc.), fillers, additives and other substances, which is mainly used in the printing and packaging industry, and is one of the most important printing materials in the printing industry.
Ink products can be divided into offset (lithographic) ink, gravure ink, letterpress ink, flexographic ink, screen printing (silkscreen) ink, pad printing ink and inkjet ink, etc. according to different printing methods. According to the different substrates can be divided into paper ink, plastic ink, metal ink, glass ink, ceramic ink and fabric printing ink. According to different drying methods can be divided into volatile drying ink, penetration drying ink, oxidation drying ink, heat curing ink, light curing ink and electron beam curing ink. In addition, inks used for anti-counterfeiting and special purposes include photosensitive inks, heat-sensitive inks, pressure-sensitive inks, foaming inks, scented inks, conductive inks, magnetic inks, liquid crystal inks, jet inks and microcapsule inks.
Printing on the use of representative ink drying method varies according to the type of printing, mainly volatile drying, penetration drying, oxidation polymerization drying, heat curing and UV / EB curing and other ways.
1.Volatile drying
The solvent or water in the ink is evaporated and dried by heating. Solvent inks are not good for the environment because they contain VOCs. In order to make water-based solvents or high boiling point solvent ink drying must be equipped with a large oven, the corresponding energy consumption is also very large. The ink film after drying is only the ink in the solid components in the substrate attached to the formation of the strength of the ink film is also the strength of the connecting material itself.
2.Penetration drying
The solvent and water in the ink and other low-viscosity components penetrate into the substrate material, resin, pigment and other solid components attached to the surface of the substrate drying method. This type of drying ink can be used for paper type porous absorbent materials, but can not be used for non-permeable materials (such as plastics, etc.). The penetration drying method is used as a drying method for newspaper printing, with a short drying time and no need for drying equipment. When using this type of ink for color printing, the ink needs to be allowed to dry without losing color after being printed on the substrate.
3.Oxidation polymerization drying
Oxidative polymerization type ink uses linseed oil and soybean oil and other fats with double bonds as connecting material, which can dry with the oxygen in the air by oxidative polymerization reaction. With the penetration of the same drying method, although the drying does not require equipment and does not consume energy, but requires a certain amount of drying time, can not immediately enter the next process. In addition, powder coating is performed to prevent the backside from sticking to the dirt, which can cause environmental problems during operation.
4.Heat curing
Heat-curing ink using epoxy resins, polyurethane resins and amino resins and other heat-curing crosslinking resins as a connecting material, while matching the heat curing agent, for the two-component system, when used in a certain proportion of mixing and stirring, infrared baking channel or hot air heating, thermal crosslinking occurs and curing of the film. Heat-curing ink performance is excellent, but energy consumption, and solvent volatilization, not environmentally friendly, so many varieties of energy-saving and environmentally friendly UV ink replaced.
5.UV / EB curing
UV / EB curing type ink contains active materials, cured by ultraviolet light or electron beam irradiation. Because it does not contain solvents and other VOC components, the environmental impact is small, can also be used for plastics and other non-absorbent substrate materials. UV / EB is instant curing, printing can be immediately transferred to the next process. UV / EB ink does not undergo ultraviolet (UV) or electron beam (EB) irradiation will not be cured, and therefore will not adhere to the printing machine.
UV ink dries instantaneously, so it has the advantage of being able to be transferred to the next process immediately after printing. Since UV irradiation is required, it consumes more energy than oxidative polymerization and osmotic drying, but the drying energy consumption is much smaller than that of volatile drying inks or heat-curing inks that use large ovens. The printed ink film is very tough because it is formed by the cross-linking reaction of UV/EB materials. In addition, the ink is not absorbed by the substrate and does not require heating, so it can be used on a wide range of substrates.
UV ink is an environmentally friendly ink because it has no solvent emission, and it has many advantages compared with ordinary ink:
① No solvent emissions, both environmental protection and safety;
② high productivity, printing speed of up to 100 ~ 400m/min, fiber optic ink can be as high as 1500 ~ 3000m / min;
③ fast curing, so the print is dry, stacking will not be due to the ink is not dry and stain each other, so no powder spraying, so the printing machine and workshop environment is clean, no dust pollution;
④ The ink is cured immediately after printing, the dot is not enlarged, and the ink does not penetrate into the paper, so the print quality is excellent, and the color saturation, color strength and clarity of the print are significantly better than ordinary ink;
⑤ It can be processed online and is suitable for assembly line production;
⑥ suitable for heat-sensitive substrate printing.
The main problems of UV ink at present are:
① more expensive, affecting the popularization and application;
② part of the raw materials (active diluents, photoinitiators) have odor, toxicity or skin irritation, affecting the application of food, pharmaceuticals and children’s products packaging printing;
③ Instantaneous curing, resulting in volume contraction, so that the ink layer increases the internal stress, reducing the adhesion to the substrate, affecting the application of products such as metal;
④ need to be protected from light, low temperature (<30 ℃) under the conditions of transportation and storage.
UV ink used in the connecting material is oligomer, mainly with light-curing properties of acrylic resins; UV ink does not use solvents or oils, but active diluent, mainly with light-curing properties of acrylic polyfunctional esters; UV ink catalyst for the photoinitiator, UV light irradiation can be a photochemical reaction that produces free radicals or cations, thereby triggering the polymerization and polyfunctional esters of acrylic acid oligomers and acrylic acid. Acrylic oligomer and acrylic polyfunctional ester polymerization and crosslinking curing, so that the ink dry.