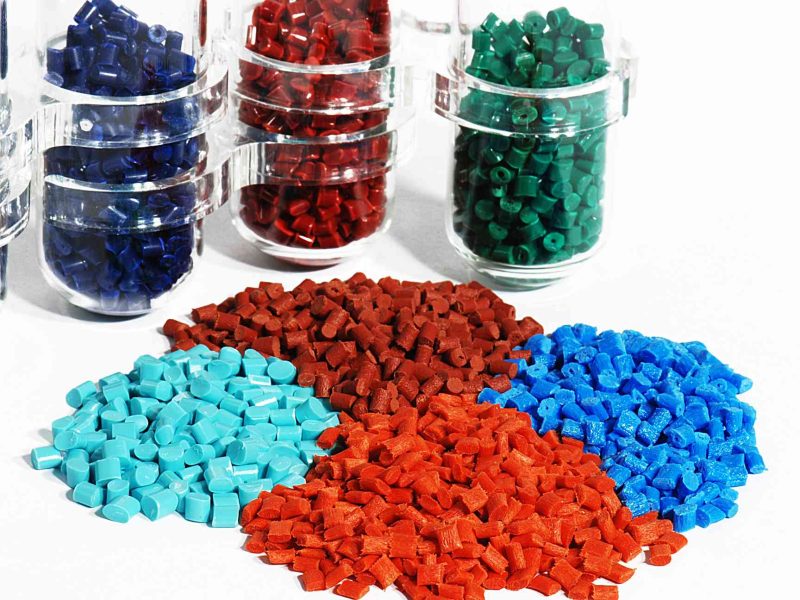
Optimizing Hyaluronic Acid Hydrogels: Small-Batch Cross-Linking with BDDE
Enhancing the Future of Hyaluronic Acid Hydrogels: Innovative Mixing Approaches for Optimal Cross-Linking with BDDE
Hyaluronic acid (HA) hydrogels cross-linked with 1,4-butanediol diglycidyl ether (BDDE) have become indispensable in various industries, ranging from cosmetics to healthcare. These hydrogels boast enhanced stability, biocompatibility, and customization, making them highly suitable for dermal fillers, controlled drug release systems, wound care, and even regenerative medicine. However, a challenge exists: optimizing cross-linking efficiency with minimal BDDE usage to create safer and more durable hydrogels.
Traditional and newer methods for cross-linking hydrogels often vary in complexity, production time, and effectiveness. This article explores the impact of two different mixing strategies for preparing BDDE-HA hydrogels: large-batch and small-batch mixing. The differences between these methods offer insight into how specific processes can influence the quality and performance of the final product, especially in terms of stability, degradation, and structural density. Let’s dive into how these methods stack up and how small-batch mixing could represent a step forward in hydrogel production.
Why BDDE is the Preferred Cross-Linker for HA Hydrogels
To understand why cross-linking efficiency matters, it’s crucial to explore the role of BDDE in hyaluronic acid hydrogels. BDDE is a di-epoxide cross-linking agent that forms strong, stable bonds with HA, an essential biopolymer known for its hydrating and viscoelastic properties. By bonding with HA, BDDE creates a hydrogel network that retains HA’s natural moisture-retaining properties while adding structural integrity. This strengthened structure ensures the hydrogel resists degradation, even when exposed to enzymes like hyaluronidase, which are naturally present in the body.
Reducing the amount of BDDE used is a major goal, as it minimizes potential toxicity and aligns with safety standards in medical and cosmetic applications. Achieving this goal without compromising hydrogel quality requires efficient cross-linking methods—hence the need to examine different mixing approaches.
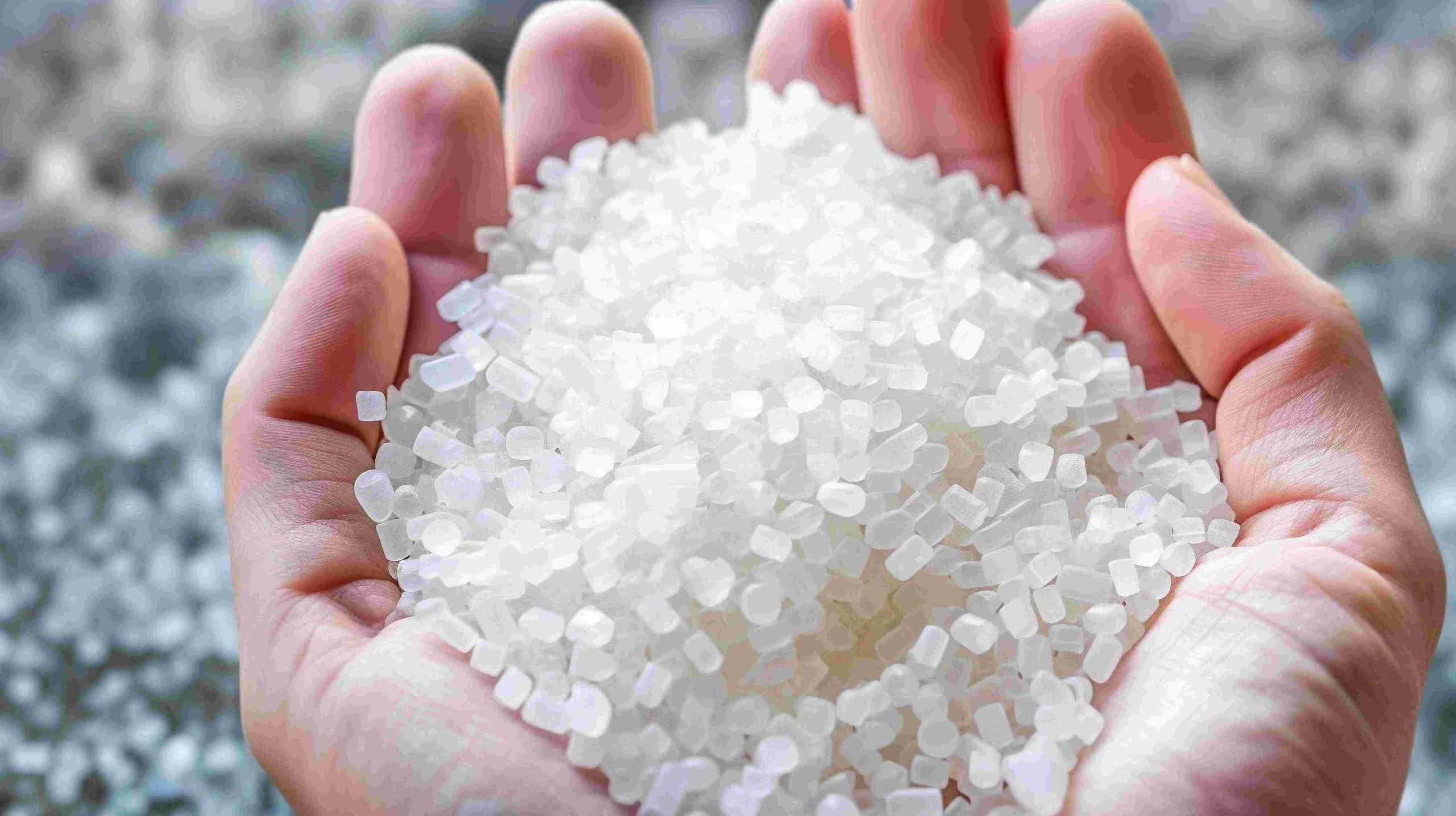
Comparing Two Mixing Strategies: Large-Batch vs. Small-Batch Approaches
- Large-Batch Mixing:
In the large-batch approach, HA and BDDE quantities are combined in a single container and cross-linked as one unified reaction. This method is straightforward and typically cost-effective, often making it the first choice for large-scale production. However, with all ingredients combined at once, achieving uniform cross-linking across the entire batch can be challenging. Variability in cross-linking density may arise, leading to sections with differing structural properties, which can affect the hydrogel’s performance and durability. - Small-Batch Mixing:
The small-batch approach divides HA and BDDE into multiple portions, allowing each portion to be mixed separately at varied HA/BDDE ratios before combining them into a final reaction mixture. This method offers better control over the cross-linking reaction by enabling customized adjustments for each smaller batch. The result is a more uniform cross-linked structure with consistent density across the hydrogel, potentially enhancing the material’s stability, strength, and longevity.
Findings: Key Benefits of Small-Batch Mixing for BDDE-HA Hydrogels
A series of tests on hydrogels prepared via both approaches shed light on several advantages offered by small-batch mixing:
Greater Cross-Linking Efficiency and Structural Integrity
Small-batch mixing results in a denser network within the hydrogel, as confirmed by electron microscopy studies. This density indicates a higher degree of HA-HA entanglement and more effective BDDE bonding. A denser network equates to a stronger, more resilient hydrogel with improved load-bearing capacity and less susceptibility to mechanical stress.
Enhanced Stability and Resistance to Enzymatic Degradation
In degradation tests, small-batch hydrogels showed better resistance to hyaluronidase—an enzyme that can break down HA. This increased durability is crucial in applications where long-lasting effects are desired, such as in dermal fillers or medical devices placed inside the body. With greater enzyme resistance, small-batch hydrogels are likely to retain their structure and performance over a longer period.
Controlled Swelling Behavior
When soaked in distilled water, large-batch hydrogels exhibited a higher swelling ratio compared to small-batch hydrogels. This suggests that small-batch hydrogels can maintain dimensional stability better in moist environments, which is essential for applications where precise control over hydrogel expansion is critical. In a controlled buffer solution, however, both hydrogels showed similar swelling behavior, underscoring that environmental conditions play a role in swelling properties.
Efficient Use of BDDE
Due to the more uniform distribution of BDDE in the small-batch approach, less cross-linker is required to achieve optimal structural integrity. This reduction in BDDE usage not only reduces production costs but also enhances the biocompatibility and safety profile of the hydrogel, making it more appealing for medical and cosmetic applications.
Improved Structural Uniformity
SEM imaging revealed that small-batch hydrogels have smaller pore sizes and a denser internal structure compared to large-batch hydrogels. This microstructure difference contributes to improved mechanical properties, which is advantageous for applications requiring structural integrity, like tissue engineering scaffolds and implants.
Consistency in Chemical Composition
Chemical analysis (FTIR and NMR) confirmed the presence of characteristic peaks in both large- and small-batch hydrogels, indicating successful BDDE cross-linking. However, the small-batch approach showed a higher degree of modification, implying a more thorough reaction between HA and BDDE. This consistency in chemical composition directly correlates with the hydrogel’s reliability and functionality.
Applications of Small-Batch BDDE-HA Hydrogels
Given the improved properties of small-batch BDDE-HA hydrogels, they are particularly suited for applications where longevity, safety, and structural integrity are paramount. Here’s how they apply across industries:
Dermal Fillers: The enhanced stability and controlled swelling behavior make these hydrogels ideal for injectable fillers that require precise volumization without unwanted expansion.
Drug Delivery Systems: Small-batch hydrogels’ structural consistency enables controlled release of therapeutic agents, making them useful for sustained-release drug delivery platforms.
Wound Care and Regenerative Medicine: In wound care, a stable hydrogel can provide a moist healing environment for extended periods, promoting tissue repair. Additionally, the hydrogel’s biocompatibility and structural integrity make it a suitable scaffold for regenerative medicine applications.
Implants and Medical Devices: The dense network structure and high degree of cross-linking contribute to mechanical durability, making small-batch BDDE-HA hydrogels suitable for load-bearing applications, such as soft tissue implants or coatings for medical devices.
Conclusion: Small-Batch Mixing as a Step Forward in Hydrogel Technology
In summary, the small-batch mixing approach offers a clear path toward producing BDDE-HA hydrogels with superior performance characteristics. By creating a more homogeneous and stable network, this method not only enhances the structural integrity of the hydrogel but also reduces the need for higher BDDE concentrations. The benefits of small-batch mixing extend across multiple applications, from cosmetic fillers to advanced medical devices, making it a highly versatile and valuable technique for the future of hydrogel production.
This approach aligns with a growing demand for high-quality, safe, and effective hydrogel products that meet the rigorous standards of healthcare and cosmetic industries. As manufacturers continue to refine cross-linking techniques, small-batch mixing represents an important innovation for delivering hydrogels with enhanced functionality and broader applications, supporting the advancement of products that improve quality of life.