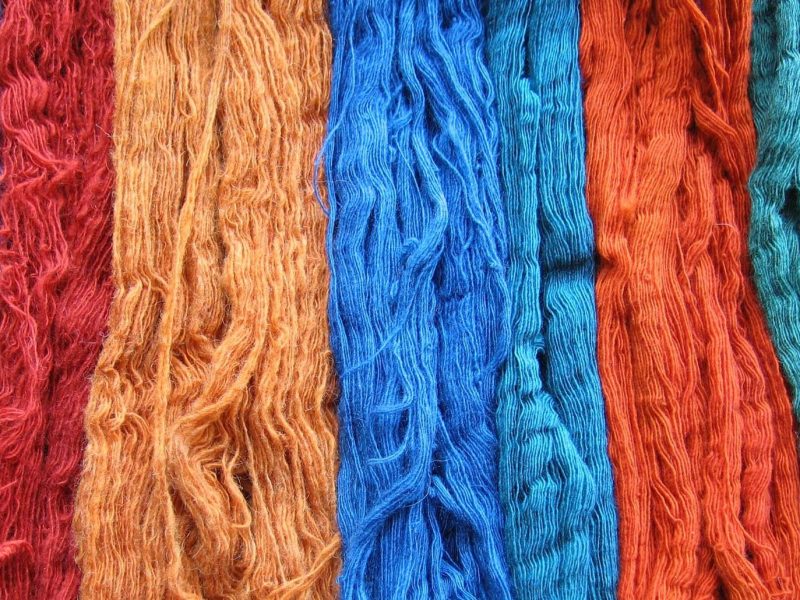
Effect of Dicumyl Peroxide on Pandanwangi Fiber Reinforced Polyethylene Composites
Synthesis and Properties of Pandanwangi Fiber Reinforced Polyethylene Composites: A Study of the Effect of Dicumyl Peroxide on Mechanical Properties
Introduction
The increasing demand for environmentally friendly and sustainable materials has spurred the development of composite materials that combine natural fibers with synthetic polymers. In this context, natural fiber-reinforced polymer composites (NFPCs) have garnered significant attention due to their renewable, biodegradable nature, and potential to reduce the environmental impact of synthetic materials. Pandanwangi, a type of natural fiber, has been explored as a reinforcement in polymer matrices, especially polyethylene (PE), a widely used thermoplastic polymer.
The main objective of this study is to examine the synthesis and properties of Pandanwangi fiber-reinforced polyethylene composites with varying concentrations of dicumyl peroxide (DCP) as a crosslinking agent. DCP is commonly employed to enhance the mechanical properties of polymer matrices through crosslinking, which can significantly improve the composite’s strength, stability, and durability. In this essay, we will explore the effects of varying DCP concentrations on the mechanical properties of Pandanwangi fiber-reinforced polyethylene composites, providing a detailed analysis of the synthesis process, material characterization, and the implications of the findings.
Materials and Methods
Materials
Pandanwangi Fiber: Pandanwangi, a natural cellulose fiber, was used as a reinforcement filler in the composites. Cellulose fibers are known for their high strength-to-weight ratio, biodegradability, and renewability, making them ideal for reinforcing synthetic polymers.
Polyethylene (PE): The polymer matrix used in this study was polyethylene, a widely used thermoplastic due to its excellent chemical resistance, ease of processing, and cost-effectiveness.
Dicumyl Peroxide (DCP): DCP was employed as a crosslinking agent to enhance the adhesion between the Pandanwangi fiber and the polyethylene matrix. The concentration of DCP was varied to investigate its impact on the mechanical properties of the composites.
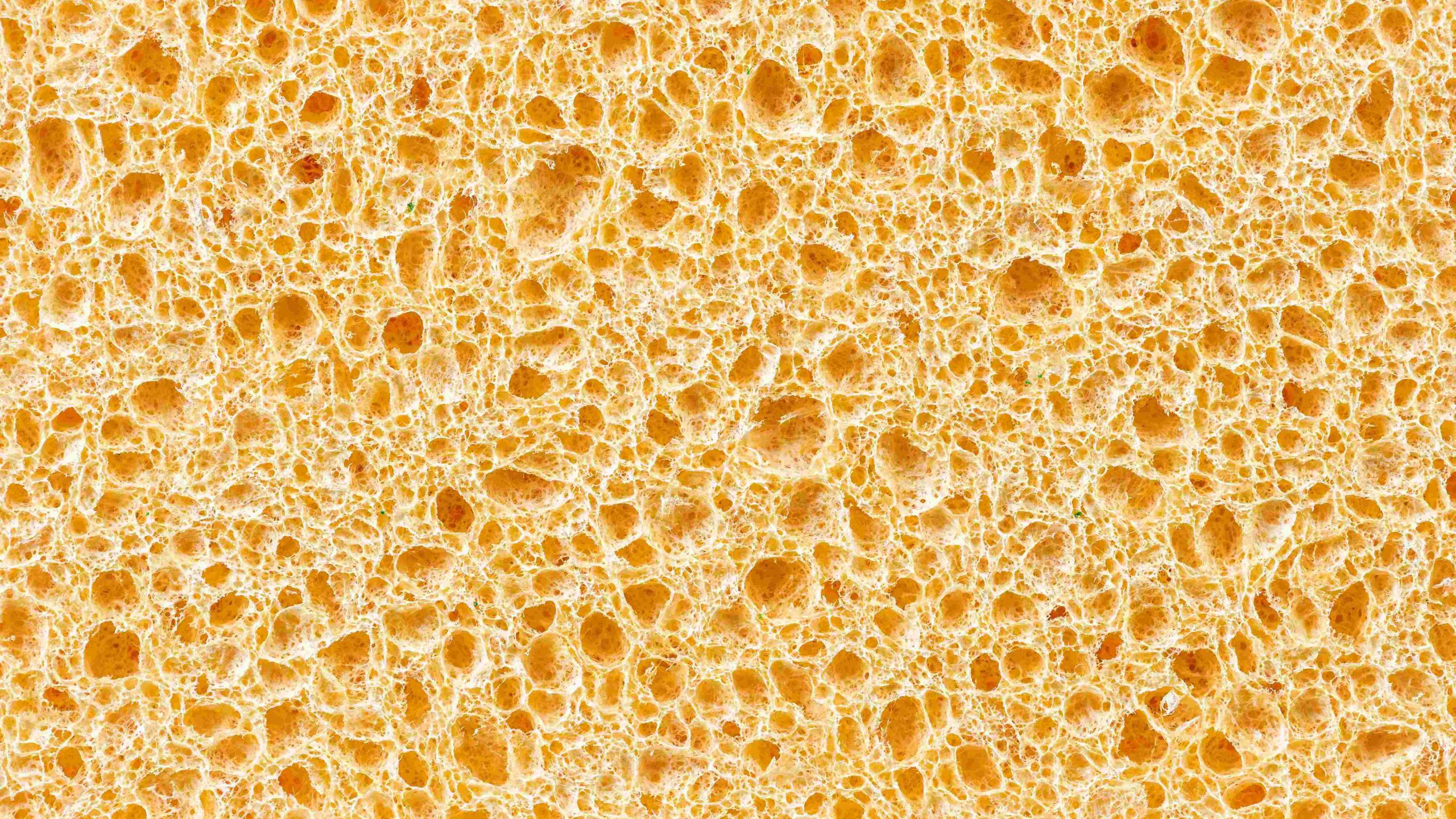
Fabrication of Composites
The composites were fabricated using the hot-press technique, a widely used method for producing polymer composites. In this process, Pandanwangi fibers were incorporated into the polyethylene matrix, with the fiber content being fixed at 10% volume fraction. DCP was added in varying amounts (1%, 2%, 3%, and 4% by weight) to induce crosslinking of the polymer chains. The mixture was then hot-pressed into sheets, which were subsequently cooled and cut into standardized specimens for mechanical testing, as per ASTM standards.
Mechanical Testing
The mechanical properties of the composites were evaluated through a series of standard tests to determine tensile strength, bending strength, and impact strength. These properties are crucial for assessing the performance of the composites under different stress conditions.
Tensile Strength: Tensile testing measures the resistance of a material to breaking under tension, providing valuable information about the material’s strength and elasticity.
Bending Strength: Bending tests measure the ability of a composite to resist deformation under load, which is important for assessing its structural integrity in practical applications.
Impact Strength: Impact testing evaluates the ability of a composite to absorb energy when subjected to a sudden force or shock, indicating the material’s toughness.
Surface Morphology Analysis
The surface morphology of the composites was analyzed using scanning electron microscopy (SEM). SEM provides high-resolution images of the composite’s surface, allowing for an in-depth analysis of the fiber-matrix interaction and the distribution of Pandanwangi fibers within the polyethylene matrix. This analysis helps to explain the observed mechanical properties of the composites and provides insights into the effects of DCP crosslinking.
Results and Discussion
Effect of DCP on Mechanical Properties
The addition of DCP to the Pandanwangi fiber-reinforced polyethylene composites significantly affected the mechanical properties, with the highest tensile, bending, and impact strength observed at a DCP concentration of 4%.
Tensile Strength: The tensile strength of the composites increased with the addition of DCP up to 4%, where it reached its peak value. This improvement can be attributed to the enhanced crosslinking between the polyethylene molecules, which increases the polymer network’s rigidity and strength. DCP facilitates the formation of covalent bonds between the polymer chains, resulting in a more stable and durable composite. At higher DCP concentrations (above 4%), the tensile strength decreased, possibly due to overcrosslinking, which could lead to the formation of a brittle network.
Bending Strength: Similar trends were observed for bending strength, where the composite with 4% DCP exhibited the highest resistance to bending. This indicates that the crosslinking effect provided by DCP improved the rigidity and structural integrity of the composite, making it less prone to deformation under bending stress. As with tensile strength, higher concentrations of DCP resulted in reduced bending strength, which may be a consequence of excessive crosslinking leading to brittleness.
Impact Strength: Impact strength, a critical property for applications requiring durability and resistance to sudden impacts, also showed a significant increase with 4% DCP. This enhancement is attributed to the improved adhesion between the Pandanwangi fiber and the polyethylene matrix, as well as the better distribution of fibers within the polymer. At higher DCP concentrations, the composite’s impact strength decreased, suggesting that excessive crosslinking may hinder the ability of the material to absorb energy efficiently.
Fiber-Matrix Interaction and SEM Analysis
The scanning electron microscopy (SEM) analysis provided valuable insights into the morphology of the composites and the interfacial bonding between the Pandanwangi fiber and the polyethylene matrix. SEM images revealed that the addition of DCP improved the adhesion between the cellulose fibers and the polymer matrix, particularly at 4% DCP concentration.
The Pandanwangi fibers were observed to be more uniformly distributed within the polyethylene matrix, and there was clear evidence of a stronger fiber-matrix bond, which is consistent with the improved mechanical properties observed. This enhanced adhesion is crucial, as it prevents fiber pullout and ensures better load transfer between the fiber and the matrix, which directly influences the composite’s strength.
At higher DCP concentrations, SEM images showed some signs of overcrosslinking, with polymer chains forming an excessively dense network. This could explain the reduction in mechanical properties observed at higher DCP concentrations, as the material became more brittle and less able to distribute stress effectively.
Comparison with Other Natural Fiber-Reinforced Composites
In the context of natural fiber-reinforced composites, many studies have highlighted the role of crosslinking agents in improving the mechanical properties of the composites. While DCP has been used in a variety of polymer systems, its application in Pandanwangi fiber-reinforced polyethylene composites is relatively novel. Previous studies have shown that natural fibers such as jute, hemp, and kenaf can significantly enhance the properties of polyethylene composites, but the use of DCP as a crosslinking agent in these systems is less common.
The results of this study indicate that Pandanwangi fibers are a promising reinforcement for polyethylene composites, and that DCP can effectively improve the composite’s mechanical properties by enhancing the fiber-matrix adhesion and facilitating polymer chain crosslinking. However, the optimal concentration of DCP for maximum performance is 4%, and further studies may be needed to explore the long-term stability and durability of these composites under various environmental conditions.
Conclusion
This study has successfully demonstrated that the incorporation of Pandanwangi fiber into a polyethylene matrix, combined with the use of dicumyl peroxide (DCP) as a crosslinking agent, significantly enhances the mechanical properties of the resulting composites. The best performance was observed at a DCP concentration of 4%, where the composites exhibited the highest tensile, bending, and impact strength. The SEM analysis revealed improved fiber-matrix adhesion, which contributed to the enhanced mechanical properties.
While the use of DCP in natural fiber-reinforced polyethylene composites shows great potential, further research is needed to explore the effects of other crosslinking agents, fiber treatments, and processing techniques on the properties of these composites. Additionally, studies investigating the environmental impact and biodegradability of these materials would be valuable in assessing their suitability for various applications in the automotive, construction, and packaging industries.
This study contributes to the growing body of knowledge on the use of natural fibers and crosslinking agents in the development of sustainable and high-performance polymer composites, providing a foundation for future research in this field.