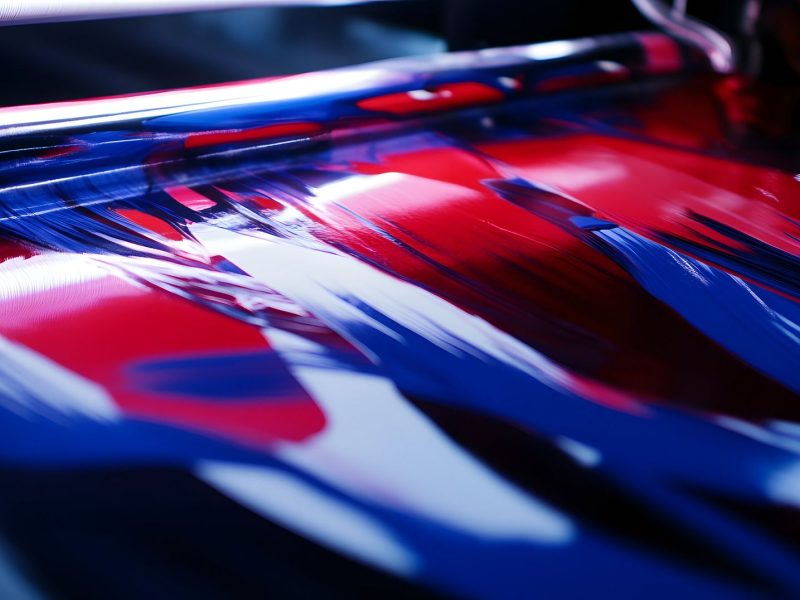
UV Curing: A Comprehensive Guide to the Future of Production
In the ever-evolving world of industrial manufacturing, speed, efficiency, and sustainability are key drivers of innovation. UV curing stands out as a transformative technology that meets these demands, revolutionizing how inks, coatings, and adhesives are processed. This article explores the fundamentals of UV curing, its components, benefits, and wide-ranging applications, offering insights into why it’s becoming the go-to solution for modern production.
What is UV Curing?
UV curing, or ultraviolet curing, is a photochemical process where ultraviolet (UV) light triggers a rapid reaction in specialized solutions—such as inks, coatings, or adhesives—causing them to polymerize and harden almost instantly. Unlike traditional drying methods that rely on heat, UV curing leverages the power of UV light to initiate this transformation, making it exceptionally fast and well-suited for high-speed production environments.
The process begins when UV light interacts with a curing solution applied to a substrate. This interaction sets off a chain reaction that converts the liquid solution into a solid, durable material in mere seconds. This efficiency has made UV curing a game-changer across industries seeking to optimize their workflows.
The Science of UV Curing Solutions
At the core of UV curing are carefully formulated solutions composed of several key ingredients:
- Oligomers: These form the structural backbone of the cured material, determining properties like hardness, flexibility, and resistance to scratches or wear. For example, in automotive coatings, oligomers ensure a tough, glossy finish that withstands the elements.
- Monomers: Acting as cross-linkers, monomers adjust the solution’s viscosity to suit specific application methods, such as spraying or rolling. They enhance the final product’s strength by linking oligomers together.
- Additives: These include pigments for color or stabilizers to improve performance. In bottle printing, additives ensure vibrant, long-lasting designs.
- Photoinitiators: The catalysts of the process, photoinitiators absorb UV light and generate free radicals, kickstarting polymerization. Though they make up just a small percentage of the solution, their role is critical.
When UV light strikes the photoinitiators, it triggers a rapid bonding of monomers and oligomers, forming a robust polymer network. This reaction’s speed and lack of heat requirement set UV curing apart from traditional methods.
Understanding UV Light and Lamp Systems
UV light occupies a segment of the electromagnetic spectrum between visible light and X-rays, characterized by shorter wavelengths and higher energy. This energy is what drives the curing process.
Two main types of UV lamp systems dominate industrial applications:
- Arc Lamp Systems:
These use tubular quartz lamps filled with mercury and rare gases. When an electric discharge excites the mercury, it emits UV light across a broad spectrum. Arc lamps are reliable and widely used, offering flexibility for various substrates. For instance, in metal decoration, arc lamps ensure even curing for intricate designs. - Microwave-Powered Electrodeless Systems:
These lamps, also quartz-based, are powered by microwave energy that excites mercury into a plasma state, producing UV light. They boast longer lamp life, fewer consumable parts, and no need for shutters, making them ideal for continuous production lines. In flooring applications, their consistent output ensures deep, uniform curing.
A complete UV curing system includes the lamp housing, a power supply (or ballast for arc lamps), a cooling fan, and cables. The lamp housing features a curved reflector that directs UV light onto the substrate, either for broad exposure or focused, high-intensity curing. High peak irradiance—measured in watts per square centimeter—enhances curing speed and depth, ensuring strong adhesion and durability.
Why Choose UV Curing Over Traditional Methods?
Before UV curing, industries relied on thermal drying with large ovens or hot air blowers. While effective, these methods posed challenges:
- Environmental Impact: Thermal drying released volatile organic compounds (VOCs) and hazardous air pollutants (HAPs), contributing to air pollution and health risks.
- Space and Cost: Large ovens consumed significant factory space and energy, driving up operational costs.
- Time: Drying could take minutes or hours, slowing production.
UV curing addresses these issues with compelling advantages:
- Faster Curing: Solidification happens in seconds, not minutes, boosting throughput. For example, a printing press using UV-cured inks can produce thousands of labels per hour.
- Energy Efficiency: UV systems use less power than thermal ovens, cutting energy bills.
- Eco-Friendly: With 100% solid formulations, UV curing eliminates solvent emissions, aligning with green manufacturing goals.
- Compact Design: UV lamps require minimal space, freeing up factory floors.
- Superior Quality: Products exhibit sharper prints and tougher coatings. In sporting goods, UV-cured finishes on golf balls enhance durability and aesthetics.
Industrial Applications of UV Curing
UV curing’s versatility shines in its broad applicability. It enhances both flat and 3D products across numerous sectors:
- Automotive: UV-cured coatings protect headlights and body panels, offering resistance to UV degradation and scratches. A German automaker reported a 25% production increase after adopting UV curing for interior trim.
- Bottle and Cup Printing: UV inks deliver vivid, smudge-proof designs on glass and plastic containers, ideal for beverage branding.
- Metal Decoration: Used for coating rims and cans, UV curing ensures a sleek, durable finish.
- Flooring: UV-cured polyurethane coatings provide high-gloss, wear-resistant surfaces for homes and offices.
- Pipes and Tubes: Protective coatings extend lifespan by preventing corrosion.
- Plastics: From toys to electronics, UV curing enhances plastic durability and appearance.
- Printing and Converting: UV inks enable high-speed, high-resolution printing on packaging, such as food wrappers.
- Sporting Goods: Items like fishing rods and tennis rackets benefit from UV-cured finishes.
- Wood: UV coatings preserve wood’s natural beauty while adding protection.
Real-World Examples
- Packaging Innovation: A U.S.-based packaging firm switched to UV curing for its flexible packaging line. The result? A 40% reduction in drying time and a 15% increase in print clarity, allowing them to meet tight deadlines for a major retailer.
- Automotive Efficiency: A Japanese car manufacturer implemented microwave-powered UV lamps for dashboard coatings. This reduced curing time from 10 minutes to 8 seconds, slashing energy use by 30% and improving output.
The Evolution and Future of UV Curing
UV curing’s rise reflects a shift toward sustainable, efficient manufacturing. As industries face stricter environmental regulations and rising energy costs, UV technology offers a forward-thinking solution. Advances in lamp design and curing formulations promise even faster speeds and broader applications, from 3D printing to medical device coatings.
Conclusion
UV curing is more than a technological trend—it’s a cornerstone of modern production. Its ability to deliver rapid, high-quality results while minimizing environmental impact makes it indispensable. Whether you’re in automotive, printing, or beyond, UV curing offers a path to smarter, greener manufacturing.