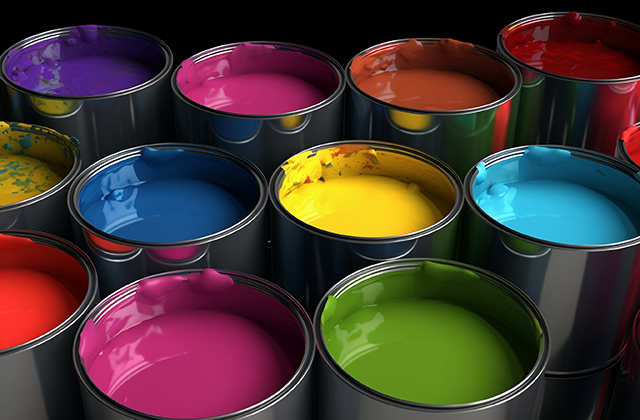
The Unseen Catalysts: Exploring the Diverse and Essential Uses of Photoinitiators
In the realm of materials science and manufacturing, the ability to transform a liquid formulation into a solid, durable material on demand is a cornerstone of countless technologies. While heat has traditionally been the primary driver for curing processes like polymerization and cross-linking, a more nuanced, efficient, and often superior method relies on the power of light. Central to this light-driven transformation are unassuming yet critical molecules known as photoinitiators. These compounds act as the catalysts, absorbing specific wavelengths of light (typically ultraviolet or visible) and converting that light energy into chemical energy, initiating rapid polymerization or cross-linking reactions. The result, often termed “photocuring” or “UV curing,” offers remarkable advantages in speed, energy efficiency, spatial control, and environmental profile, leading to the indispensable role of photoinitiators across an astonishingly broad spectrum of industries and applications.
Understanding the Mechanism: The Spark of Polymerization
Before delving into their uses, it’s helpful to understand how photoinitiators work. At their core, they are molecules designed with specific chromophores that allow them to absorb photons of light energy efficiently. Upon absorbing this energy, the photoinitiator molecule becomes electronically excited. This excited state is highly unstable and rapidly undergoes one of two primary processes to generate reactive species capable of initiating polymerization:
-
Type I Photoinitiators (Cleavage Type): Upon light absorption, these molecules undergo intramolecular bond cleavage (photolysis), directly generating two free radicals. These radicals are highly reactive and immediately attack the double bonds of monomers or oligomers (the building blocks of the polymer) present in the formulation, initiating a chain reaction that rapidly builds the polymer network. Examples include benzoin ethers, acyl phosphine oxides (like TPO), and hydroxy ketones. They are known for high efficiency and speed.
-
Type II Photoinitiators (Abstraction Type): These photoinitiators do not directly generate radicals themselves upon excitation. Instead, the excited photoinitiator molecule interacts with a second molecule, known as a co-initiator or synergist (often an amine or thiol), through a process like hydrogen abstraction or electron transfer. This interaction generates the initiating free radicals from the co-initiator molecule. Examples include benzophenone/amine systems and thioxanthone derivatives. While sometimes requiring a co-initiator, Type II systems can offer advantages in specific applications, such as reduced oxygen inhibition effects at the surface.
Beyond radical polymerization, some photoinitiators, known as photoacid generators (PAGs) or photobase generators (PBGs), produce strong acids or bases upon irradiation. These are used to initiate cationic polymerization (e.g., for epoxies and vinyl ethers) or anionic polymerization, respectively, expanding the range of chemistries accessible via light curing.
The Ubiquitous Applications: Where Light Meets Material
The unique advantages conferred by photoinitiator-driven curing – speed (seconds to minutes vs. hours), low energy consumption (light sources vs. large ovens), room temperature processing (protecting sensitive substrates), solvent-free formulations (reducing VOC emissions), and precise spatial control (using masks or focused light) – have led to their adoption in numerous fields:
-
Coatings and Inks: This is arguably one of the largest application areas.
- Wood Coatings: UV-curable varnishes and lacquers provide exceptional scratch resistance, chemical resistance, and high gloss finishes for furniture, flooring, and cabinetry, often cured almost instantaneously on automated lines.
- Metal Coatings: Protective and decorative coatings for cans, pipes, and automotive components benefit from the speed and durability of UV curing.
- Plastic Coatings: Enhancing the surface properties (e.g., scratch resistance) of plastics for automotive headlamps, mobile phone casings, and optical discs.
- Overprint Varnishes (OPVs): Applied over printed materials (packaging, labels, book covers) to provide gloss, protection, and tactile effects, curing rapidly on press.
- Printing Inks: UV-curable inks are used extensively in offset, flexography, screen printing, and increasingly in inkjet printing. They offer instant drying on diverse substrates (paper, plastic, metal, glass), sharp dot definition, high print speeds, and vibrant colours. Their solvent-free nature is a significant environmental advantage.
-
Adhesives: Light-curing adhesives offer “cure-on-demand” capabilities, ideal for assembly processes.
- Electronics: Bonding components to printed circuit boards (PCBs), encapsulating sensitive microelectronics, wire tacking, and sealing displays. The speed and precision are critical.
- Medical Device Assembly: Bonding needles to hubs, assembling catheters, hearing aids, and diagnostic equipment. Biocompatible formulations are essential here, often requiring specific, highly purified photoinitiators. The absence of heat protects delicate components.
- Glass and Plastics Bonding: Structural bonding in applications ranging from decorative glass lamination to assembling plastic housings, often where at least one substrate is transparent to UV/visible light.
- Temporary Bonding/Masking: Used in manufacturing processes where a component needs to be held temporarily and later released, or an area masked during processing.
-
Dental Materials: Photopolymerization revolutionized dentistry.
- Composite Fillings: Resin-based composites containing photoinitiators (often camphorquinone, CQ, sensitive to blue light) are placed in a tooth cavity and cured layer by layer using a dental curing light. This allows for tooth-coloured restorations with excellent bonding and wear characteristics.
- Sealants: Applied to the pits and fissures of teeth to prevent decay, cured rapidly in the mouth.
- Orthodontic Adhesives: Used to bond brackets to teeth for braces, offering quick setting times.
- Denture Bases and Repair Materials: Light-cured resins are used for fabricating and repairing dentures.
-
Electronics and Microfabrication: Precision is paramount in this sector.
- Photoresists: Photoinitiators are fundamental components of photoresists used in photolithography – the process underpinning the manufacture of integrated circuits (microchips) and printed circuit boards. Light exposure through a mask selectively cures (negative resist) or makes soluble (positive resist) the resist material, allowing intricate patterns to be etched onto the underlying substrate. PAGs are particularly important in chemically amplified resists for high-resolution features.
- Conformal Coatings: Protecting PCBs from moisture, dust, and chemicals. UV-curable coatings offer rapid processing compared to solvent-based or heat-cured alternatives.
- Encapsulants: Protecting delicate semiconductor chips or sensors.
-
3D Printing / Additive Manufacturing: Photoinitiators are the engines driving several key 3D printing technologies.
- Stereolithography (SLA): A laser selectively cures layers of liquid photopolymer resin in a vat.
- Digital Light Processing (DLP): Similar to SLA, but uses a digital projector to cure an entire layer at once, often enabling faster build speeds.
- Material Jetting (PolyJet/MultiJet): Droplets of photopolymer resin are jetted onto a build platform and immediately cured by UV lamps, allowing for multi-material and multi-colour parts. The ability to rapidly solidify liquid resin layer by layer with high resolution relies entirely on efficient photoinitiator systems.
-
Medical and Biomedical Applications (Beyond Dental):
- Hydrogels: Photoinitiators enable the in situ formation of hydrogels for applications like wound dressings, drug delivery systems, and scaffolds for tissue engineering. Biocompatibility and controlled degradation are key considerations.
- Catheter Coatings: Creating lubricious or antimicrobial coatings on catheters.
- Manufacturing Aids: Used in the production of contact lenses and other medical devices requiring precise shaping and curing.
Challenges and Future Directions
Despite their widespread success, challenges remain. Oxygen inhibition at the surface can lead to tacky finishes, requiring nitrogen inerting or specialized formulations. Light penetration depth limits the thickness of materials that can be fully cured, especially with highly pigmented or filled systems. Some traditional photoinitiators have faced regulatory scrutiny due to concerns about migration or by-products (e.g., yellowing or potential toxicity), driving research into safer, low-migration alternatives.
The future of photoinitiators is bright, focusing on:
- Visible Light Photoinitiators: Expanding curing beyond the UV spectrum, allowing for deeper penetration, use with visible light LEDs (which are becoming more efficient and cheaper), and safer handling. This is crucial for dental and biomedical applications.
- Waterborne UV Systems: Developing photoinitiators and formulations compatible with water-based systems to further improve environmental profiles.
- LED-Specific Photoinitiators: Designing PIs optimized for the narrow emission spectra of UV-LEDs, improving efficiency and reducing energy waste.
- Low-Migration/Low-Toxicity PIs: Addressing regulatory demands, especially for food packaging, medical devices, and toys.
- Photoinitiators for Novel Chemistries: Enabling light-induced polymerization beyond traditional acrylates and epoxies, opening doors to new material properties.
- Applications in Advanced Composites and Biofabrication: Pushing the boundaries in areas like rapid composite manufacturing and precise 3D bioprinting of tissues and organs.
Conclusion
Photoinitiators are far more than simple additives; they are enabling molecules that unlock the potential of light-driven chemistry. From the glossy finish on a magazine cover to the intricate circuits in a smartphone, from a durable dental filling to a complex 3D-printed prototype, their presence is pervasive, often unseen but fundamentally essential. By converting light into chemical reactivity, they facilitate manufacturing processes that are faster, cleaner, more energy-efficient, and capable of producing materials and structures with remarkable precision and performance. As technology advances and the demand for sustainable, high-performance materials grows, the continued innovation and application of photoinitiators will undoubtedly remain a critical catalyst for progress across science and industry.