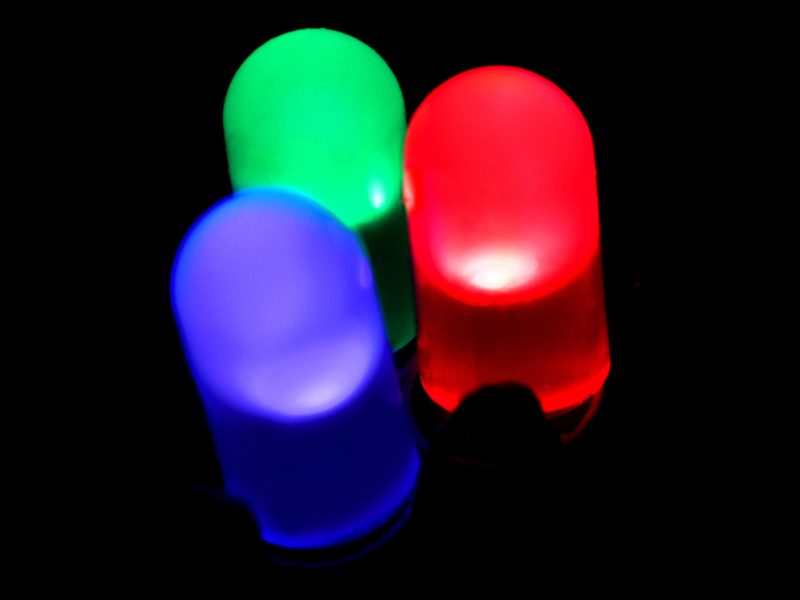
UV/Heat Dual-Curing Adhesives: The Superior Bonding Solution Combining Speed and Strength
In the relentless pursuit of manufacturing efficiency, material performance, and design innovation, the way we join components together is critical. Adhesives play a pivotal role, offering advantages over traditional mechanical fastening. For decades, UV (Ultraviolet) curing and thermal (heat) curing have been staple technologies. UV curing, with roots tracing back to photographic inventions in 1826, brought incredible speed to production lines. Thermal curing offered robustness and deep bonding. But what if you could harness the best attributes of both? Enter the era of UV/Heat Dual-Curing Adhesives – a sophisticated technology designed to overcome the limitations of single-cure methods and unlock new possibilities in assembly.
This article delves into the world of UV/Heat dual-cure systems. We’ll explore why they are becoming increasingly essential, how they work, their intricate chemical makeup, the diverse applications they serve, and the exciting future trends shaping their development. If you’re facing challenges with curing speed, shadowed areas, heat-sensitive components, or demanding performance requirements, understanding this technology could be the key to your next breakthrough.
Understanding the Need: Why Single Cure Isn’t Always Enough
While both UV and thermal curing have served industries well, each comes with inherent limitations, particularly as product designs become more complex and performance demands escalate.
The Limitations of UV-Only Curing
UV curing adhesives polymerize, or harden, almost instantaneously upon exposure to specific wavelengths of UV light. This offers significant advantages:
- Rapid Curing: Seconds, not minutes or hours.
- High Production Efficiency: Ideal for automated, high-volume assembly lines.
- Energy Savings: Less energy consumed compared to prolonged oven curing.
- Environmental Benefits: Often formulated with low or zero volatile organic compounds (VOCs).
However, UV curing isn’t a perfect solution for every scenario:
- Line-of-Sight Dependency: UV light must directly reach the adhesive. Areas hidden by components (shadowed areas) won’t cure properly, leading to potential bond failure.
- Incomplete Through-Cure: In thicker adhesive layers or highly filled/pigmented systems, the UV light intensity diminishes as it penetrates, potentially leaving the lower layers uncured or under-cured. Opaque or dark colored materials can significantly interfere with light absorption, drastically reducing curing efficiency.
- Oxygen Inhibition: The free-radical polymerization common in many UV systems (especially acrylate-based ones) can be inhibited by atmospheric oxygen at the surface. This results in a tacky or under-cured surface layer, impacting final properties and potentially requiring inert gas purging (like nitrogen) during cure, adding complexity and cost.
- Substrate Limitations: UV light must be able to pass through at least one substrate if bonding two opaque materials isn’t feasible.
The Drawbacks of Traditional Thermal Curing
Heat-cured adhesives, often epoxies, polyurethanes, or silicones, form strong, durable bonds with excellent resistance properties. They are workhorses in many demanding applications.
- Excellent Bond Strength & Durability: Often achieve superior mechanical properties and resistance to heat, water, and chemicals.
- Good Process Applicability: Can fill gaps and bond complex geometries without line-of-sight issues.
- Versatility: Wide range of formulations available for different performance needs.
But thermal curing also has significant drawbacks:
- Slow Curing Speed: Cure times can range from minutes to many hours, creating bottlenecks in production.
- High Energy Consumption: Ovens require significant energy to maintain curing temperatures, increasing operational costs.
- Thermal Stress: The heating and cooling cycles can induce stress on components, particularly problematic for delicate electronics or materials with different coefficients of thermal expansion (CTE).
- Handling Constraints: Parts often need racking or fixtures during the long cure cycle, adding complexity and space requirements.
Recognizing these individual limitations, researchers and formulators sought a hybrid approach – leading to the development of UV/Heat Dual-Curing Adhesives.
The Power of Synergy: How UV/Heat Dual-Curing Adhesives Work
Imagine having the speed of light for initial fixing and the robust power of heat for ultimate strength. That’s the core principle of UV/Heat dual-cure technology. These systems are intelligently designed to undergo a two-stage curing process:
- Stage 1: UV Cure (The “Tack and Fix” Stage): The adhesive is exposed to UV light. Photoinitiators within the formulation absorb the light energy and trigger rapid polymerization of UV-reactive components (like acrylates). This quickly sets the adhesive, fixing components in place, curing exposed areas, and providing initial handling strength. This stage leverages the primary benefit of UV curing – speed.
- Stage 2: Thermal Cure (The “Strength and Durability” Stage): After the initial UV cure, the assembly is subjected to heat. This activates latent thermal curing agents within the formulation, initiating a secondary reaction, often involving different functional groups (like epoxies). This heat-driven process ensures complete cure throughout the bond line, including shadowed areas inaccessible to UV light, and develops the final, robust mechanical and resistance properties.
Think of it like building with advanced construction blocks. The UV light acts like a rapid-setting mortar, instantly holding the blocks (components) precisely where you want them. The subsequent heat cure is like the steel reinforcement running through the structure, providing deep, unwavering strength and long-term stability.
This two-stage approach offers remarkable control. By carefully tailoring the formulation, manufacturers can achieve specific properties at each stage. The intermediate state after UV cure can be designed for specific handling or processing needs, while the final state after heat cure delivers the ultimate performance characteristics required for the application.
Deconstructing the Formulation: Key Components of UV/Heat Dual-Cure Systems
Creating a successful UV/Heat Dual-Curing Adhesive requires a sophisticated blend of ingredients, each playing a crucial role. The synergy between the UV-curable and heat-curable components is paramount.
The Resin Matrix: The Backbone of Performance
The resin forms the main structure of the cured adhesive, dictating many of its core properties like strength, flexibility, and chemical resistance.
- Polyurethane Acrylates (PUA): Commonly used in UV curing, PUAs remain valuable in dual-cure systems. They offer versatility – by selecting different polyols, isocyanates, and end-capping acrylate groups, formulators can tune properties like flexibility, toughness, and adhesion. They contribute significantly to the rapid UV-cure stage.
- Epoxy Resins: As classic thermosets, epoxy resins are often the preferred choice for the heat-curable portion of the system due to their exceptional thermal stability, mechanical strength, chemical resistance, and adhesion to a wide variety of substrates.
- Common Types: Bisphenol A (BPA) and Bisphenol F (BPF) epoxies are widely used for their balance of properties and cost-effectiveness.
- Specialty Epoxies: For higher performance demands (e.g., higher temperature resistance, improved toughness), specialty epoxies like Novolac epoxies or Glycidylamine epoxy resins are increasingly employed.
- Hybrid Structures: Some suppliers offer innovative “half-modified” epoxy acrylates. These molecules possess both an acrylate double bond (for UV reaction) and an epoxy group (for thermal reaction) on the same backbone. This structure facilitates efficient crosslinking between the two cure mechanisms, potentially leading to more homogenous and robust networks.
Igniting the Reaction: Photoinitiators for the UV Stage
These are the catalysts for the first cure stage. Photoinitiators are molecules that absorb specific wavelengths of UV light and generate reactive species (free radicals or cations) that initiate the polymerization of the UV-reactive resins (like acrylates).
- Types: Common types include free-radical photoinitiators, which are further divided into:
- Cleavage Type (Type I): Absorb UV light and break into two radical fragments.
- Hydrogen Abstraction Type (Type II): Require a co-initiator (like an amine) to generate initiating radicals.
- Selection Criteria: The key is matching the photoinitiator’s absorption spectrum to the emission spectrum of the UV light source (e.g., mercury lamps, LEDs). The choice also impacts surface vs. through-cure, yellowing, and overall curing efficiency.
- Advanced Initiators: For specific needs, such as curing thicker sections or pigmented systems, or for use with longer wavelength UV-A or even visible light LEDs, specialized large-molecule or polymeric photoinitiators are sometimes used.
Completing the Cure: Thermal Curing Agents
These components remain dormant during the UV stage and are activated by heat to drive the secondary cure, typically reacting with epoxy groups or other thermally reactive functionalities. Latency is a critical characteristic – they must not react prematurely at room temperature but activate reliably at the desired cure temperature.
- Imidazole Derivatives: Imidazoles can act as catalysts or curing agents for epoxies. Modified imidazoles (e.g., encapsulated or adduct types) offer improved storage stability (latency) at room temperature while providing efficient curing upon heating. Their fine particle size can also lead to more uniform cures without residual particles, enhancing reliability.
- Thiols (Mercaptans): Thiols play a fascinating dual role.
- In UV Curing: They are excellent chain transfer agents in free-radical acrylate polymerization. They readily donate a hydrogen atom to propagating radicals, which helps overcome oxygen inhibition at the surface, improving surface cure speed and completeness. The resulting thiyl radical can then continue the polymerization chain. This significantly enhances adhesion, toughness, and double bond conversion, especially under low-intensity UV exposure. Common examples include Pentaerythritol tetrakis(3-mercaptopropionate) (PETMP) and Trimethylolpropane tris(3-mercaptopropionate) (TMPTMP).
- In Thermal Curing: Thiol groups can also react efficiently with epoxy groups, especially when paired with tertiary amine accelerators (like DMP-30). This thiol-epoxy reaction can occur at relatively low temperatures and proceeds rapidly, offering a way to achieve fast thermal cures while enhancing adhesion and tensile strength.
- Hydrazides (Dihydrazides): Compounds like Adipic Dihydrazide (ADH), Sebacic Dihydrazide (SDH), and Isophthalic Dihydrazide (IDH) are latent curing agents for epoxies. They typically have high melting points, contributing to good storage stability. While their activation temperature is generally lower than that of dicyandiamide (DICY), they often require accelerators (similar to those used with DICY) to achieve practical cure speeds.
Enhancing Properties: Fillers and Additives
Beyond the core reactive components, various fillers and additives are incorporated to fine-tune properties:
- Inorganic Fillers: Materials like calcium carbonate (CaCO3), fumed or precipitated silica (SiO2), and titanium dioxide (TiO2) are common. They can:
- Increase viscosity and impart thixotropy (resistance to flow, good for gap filling).
- Improve mechanical properties like modulus and abrasion resistance.
- Reduce shrinkage during cure.
- Lower overall cost.
- Surface Modification: Critically, fillers often undergo surface treatment (e.g., with silanes or acrylates) to improve their compatibility with the organic resin matrix. Poor compatibility can lead to particle settling, weakened interfaces, and reduced performance. Modified fillers disperse better and bond more effectively within the cured adhesive network.
- Other Additives: Adhesion promoters, toughening agents, stabilizers, and rheology modifiers might also be included depending on the specific application requirements.
Advantages in Action: Benefits and Applications of UV/Heat Dual-Cure Adhesives
The unique two-stage curing mechanism translates into tangible benefits that are driving adoption across demanding industries.
Key Benefits:
- Speed and Strength: Combines the rapid fixing of UV with the robustness of a full thermal cure. Hypothetical data suggests potential cycle time reductions of 50-80% compared to heat-only systems in certain assembly steps.
- Complete Cure Assurance: Effectively cures shadowed areas inaccessible to UV light, ensuring bond integrity in complex geometries.
- Reduced Thermal Stress: The initial UV cure provides handling strength, potentially allowing for lower thermal curing temperatures or shorter heat cycles compared to traditional thermosets, minimizing stress on sensitive components.
- Process Flexibility: Allows for repositioning or inspection after the initial UV tack before the final, permanent heat cure.
- Enhanced Performance: Can achieve properties potentially superior to either single-cure system alone, thanks to the formation of interpenetrating polymer networks (IPNs).
Applications Across Industries:
-
Electronics: This is a major application area.
- Component Bonding: Attaching components to PCBs, especially heat-sensitive ones. UV fixes the part instantly, preventing movement during subsequent handling or reflow processes, followed by a low-temperature bake for full strength.
- Potting and Encapsulation: Protecting sensitive circuits or sensors from environmental factors. UV cures the surface quickly, while heat ensures deep cure in bulk material.
- Camera Module Assembly: Precisely aligning and bonding lenses and sensors where speed and stability are crucial.
- Example/Case Study 1: A manufacturer of wearable health monitors needed to bond a miniature, heat-sensitive biometric sensor onto a flexible PCB. UV-only cure left shadowed areas under the sensor uncured. Heat-only cure risked damaging the sensor and took too long for their automated line. A UV/Heat Dual-Curing Adhesive provided the solution: a 3-second UV exposure fixed the sensor perfectly, followed by a 30-minute cure at 80°C (well below the sensor’s damage threshold) achieved full, reliable bonding, drastically improving yield and throughput.
-
Medical Devices: Biocompatibility is often a key requirement here.
- Catheter Assembly: Bonding balloons, hubs, and tubing components.
- Needle Bonding: Securing metal cannulas into plastic hubs.
- Diagnostic Device Assembly: Assembling multi-part devices requiring precise alignment and robust, sterilizable bonds.
- Example/Case Study 2: An IV catheter manufacturer struggled with bonding the needle hub. UV cure was fast but didn’t provide sufficient long-term resistance to sterilization cycles. A heat cure was too slow. Switching to a biocompatible UV/Heat Dual-Curing Adhesive allowed rapid UV fixing for high-speed assembly, followed by a batch thermal cure that imparted excellent bond strength and resilience to repeated autoclaving, meeting stringent regulatory requirements.
-
Optoelectronics: Precision alignment is critical.
- Lens Bonding: Attaching lenses in optical assemblies.
- Fiber Optic Alignment: Fixing optical fibers precisely before permanent bonding. UV cure provides sub-micron alignment stability in milliseconds, followed by a heat cure for long-term environmental stability.
-
Automotive and Aerospace: High-performance bonding and sealing applications where reliability under harsh conditions is essential.
-
Packaging: High-speed sealing applications, potentially for tamper evidence or specialized functional packaging.
Overcoming Challenges: Addressing Curing Efficiency and Oxygen Inhibition
While powerful, dual-cure systems aren’t without challenges that skilled formulation addresses:
- Optimizing Curing Efficiency: Ensuring both the UV and thermal stages proceed effectively requires careful selection of photoinitiators matched to the UV source and appropriate thermal curing agents with the right latency and activation temperature. The resin components must be compatible and participate efficiently in their respective reactions. Fillers and pigments must be chosen and treated carefully to minimize interference with UV penetration.
- Managing Oxygen Inhibition: As mentioned, oxygen inhibition can plague the surface cure of free-radical UV systems. Dual-cure formulations often incorporate strategies like:
- Using thiol-ene chemistry, which is less sensitive to oxygen.
- Employing photoinitiators that work efficiently even in the presence of oxygen.
- Leveraging the subsequent heat cure: Even if the immediate surface experiences slight inhibition during the UV stage, the thermal cure ensures full crosslinking and hardening of the entire adhesive mass, including the surface layer. This is a significant advantage over UV-only systems where surface tackiness can be a persistent issue.
The Future is Bright (and Hot): Development Trends in Dual-Cure Technology
The field of UV/Heat Dual-Curing Adhesives is dynamic, with ongoing research focused on pushing performance boundaries and expanding applicability.
- Faster Curing Profiles: Development of thermal curing agents that activate at lower temperatures or more rapidly at moderate temperatures, further reducing thermal stress and energy consumption. Simultaneously, more efficient photoinitiator systems are sought for even faster UV tacking, possibly using lower-energy UV-LED sources.
- Enhanced Performance & Durability: Research into novel resin chemistries and modification directions aims to boost adhesion to difficult substrates, improve toughness and flexibility, increase thermal stability, and enhance chemical resistance. Silicone modification of epoxy or urethane backbones is one avenue being explored to impart greater flexibility and high/low temperature performance.
- Greater Sustainability: A strong push towards formulations based on renewable raw materials (bio-based resins), solvent-free systems, and chemistries that require less energy input for curing aligns with broader industry goals for environmental responsibility.
- Broader Application Reach: Tailoring formulations for niche applications in areas like flexible electronics, microfluidics, advanced composites, and 3D printing/additive manufacturing. Could custom UV/Heat Dual-Curing Adhesives become the go-to solution for assembling the complex, multi-material devices of tomorrow?
Partnering for Success: How Sinocurechemical Can Help
Navigating the complexities of UV/Heat Dual-Curing Adhesives – from understanding formulations to troubleshooting application issues – requires expertise. Sinocurechemical possesses extensive experience in analyzing and developing these advanced materials.
With a robust internal spectral library and a comprehensive suite of advanced analytical instruments, we employ specialized sample preparation and analysis techniques. This allows us to identify the constituent components of dual-cure adhesives, including:
- Determining the structure and monomers of various oligomers and resins.
- Identifying diverse reactive diluents and photoinitiators.
- Quantifying thermal curing agents and trace additives.
Sinocurechemical stays at the forefront of market developments, actively researching and analyzing new UV/Heat Dual-Curing Adhesive products across multiple sectors. We can perform comparative analyses to benchmark product performance and assist your company in overcoming R&D hurdles. Whether you need to understand a competitor’s product, develop a new formulation, or optimize your curing process, our expertise can help shorten your development cycle and enhance your product’s performance and reliability.
Conclusion: Embrace the Dual-Cure Advantage
UV/Heat Dual-Curing Adhesives represent a significant advancement in bonding technology. By intelligently combining the speed of UV light with the thoroughness and strength of thermal curing, they offer a versatile and powerful solution for modern manufacturing challenges. They enable faster production, accommodate complex designs with shadowed areas, reduce thermal stress on sensitive components, and deliver robust, reliable bonds for demanding applications in electronics, medicine, optics, and beyond.
As materials and product designs continue to evolve, the demand for adaptable, high-performance adhesives will only grow. UV/Heat dual-cure technology is poised to meet this demand, offering a pathway to improved efficiency, enhanced product quality, and greater design freedom.
Do you have questions about how UV/Heat Dual-Curing Adhesives could benefit your specific application? Are you facing challenges with your current bonding process?
The experts at Sinocurechemical are ready to help. We invite you to reach out and consult with us. Let our analytical capabilities and formulation insights accelerate your innovation. Contact us today to discuss your adhesive needs!