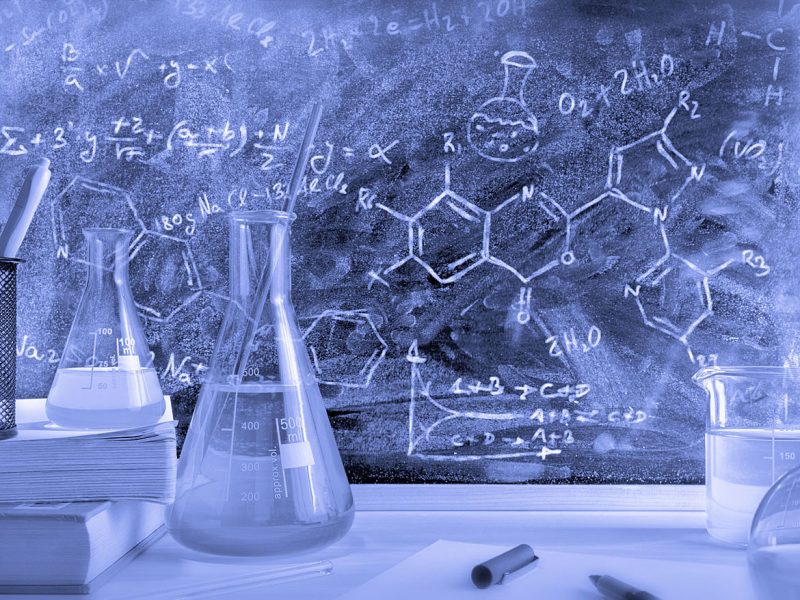
Epoxy Resin Curing Agent, or Epoxy Hardener, might sound like a technical term, but it’s the unsung hero behind many high-performance materials essential to modern industry. From durable construction structures and sophisticated electronic components to lightweight yet strong composite materials, epoxy resin curing agents play an indispensable role. They aren’t just additives; they are the core component in an epoxy system that dictates the final properties and determines the success or failure of an application.
This article will take you on an in-depth exploration of the world of epoxy resin curing agents. We’ll uncover the fundamental principles and fascinating chemical reactions behind their function, navigate their extensive classification system, discuss the key factors influencing selection, showcase their versatility in wide-ranging application fields like construction and electronics, and look ahead to future trends driven by environmental friendliness and intelligence. Whether you’re a materials engineer, product developer, or searching for the right epoxy system solution for your project, this comprehensive guide will provide valuable insights.
Understanding the Core: The Basic Principles of Epoxy Resin Curing Agents
Epoxy resins themselves are typically liquids or low-melting-point solids at room temperature. They require the addition of an epoxy resin curing agent to transform them into the hard, durable solid materials we desire. So, how does this “magic” transformation happen?
The Heart of Curing: Addition Reactions and Cross-linked Structure Formation
The basic principle lies in the chemical reaction between the epoxy resin curing agent and the epoxy groups (a three-membered ring consisting of two carbon atoms and one oxygen atom) within the epoxy resin molecules. The curing agent contains active functional groups capable of reacting with these epoxy groups. This reaction is primarily an addition polymerization process.
- Active Group Participation: Active hydrogens (usually from amine -NH or hydroxyl -OH groups on the curing agent) or other reactive functionalities attack the epoxy ring, causing it to open.
- Chain Growth and Cross-linking: This ring-opening reaction forms new chemical bonds, linking the curing agent molecules to the epoxy resin molecules. As the reaction proceeds, molecular chains grow longer. More importantly, these chains react further with each other, forming a complex, three-dimensional cross-linked structure (or network structure).
- Liquid-to-Solid Transformation: It’s this dense, interconnected cross-linked structure that “locks” the previously mobile molecules into fixed positions, imparting the cured epoxy resin with its excellent mechanical strength, heat resistance, chemical resistance, and dimensional stability. This curing mechanism is typically exothermic (releases heat), requiring control over reaction temperature and rate.
Imagine weaving countless fine threads (curing agent and epoxy resin molecules) into an incredibly strong net (the cross-linked structure). This analogy helps visualize how the liquid resin solidifies into a robust material. Understanding this curing mechanism is fundamental to grasping the function of epoxy hardeners.
A Vast Family: The Classification System of Epoxy Resin Curing Agents
The variety of epoxy resin curing agents is vast. They can be categorized in several ways based on their chemical structure, reaction mechanism, and application characteristics. Understanding these classifications helps in selecting the most suitable hardener for specific needs.
Amine Curing Agents: The Market Mainstay
Amine-based hardeners are the most widely used and diverse class of epoxy resin curing agents. They rely on the amine groups (-NH2 or -NH) in their molecules to react with epoxy groups.
- Aliphatic Amines: Examples include Ethylenediamine (EDA) and Diethylenetriamine (DETA). Pros: Fast cure at room temperature, low cost. Cons: Higher toxicity, high exotherm, cured product can be brittle. Used for quick adhesives, small castings.
- Aromatic Amines: Examples include m-Phenylenediamine (m-PDA) and Diaminodiphenylmethane (DDM). Pros: Excellent heat resistance and chemical resistance in the cured state. Cons: Higher toxicity, usually require elevated temperature cure, often darker in color. Used for high-performance composites, corrosion-resistant coatings.
- Cycloaliphatic Amines: Examples include Isophorone Diamine (IPDA). Pros: Offer a balance of properties between aliphatic and aromatic amines, good color stability, good weather resistance, relatively lower toxicity. Cons: Higher cost. Used for flooring, exterior coatings.
- Modified Amines: Amines can be chemically modified (e.g., pre-reacted with epoxy resin to form adducts, or via Mannich reactions) to reduce toxicity, improve flexibility, adjust reactivity, and enhance handling properties. This is a major area of development for amine hardeners.
Acid Anhydride Curing Agents: Preferred for Heat Resistance and Electrical Insulation
Acid anhydride curing agents (a type of Acid Curing Agent) are primarily organic anhydrides like Phthalic Anhydride (PA), Methyltetrahydrophthalic Anhydride (MeTHPA), and Hexahydrophthalic Anhydride (HHPA). They react with both the epoxy groups and hydroxyl groups present on the epoxy resin backbone.
- Pros: Cured products exhibit excellent heat resistance, outstanding electrical insulation properties, low shrinkage, and good dimensional stability.
- Cons: Slow curing speed, typically requiring prolonged curing at high temperatures (e.g., >100°C / 212°F); sensitive to moisture.
- Applications: Widely used for potting and encapsulation of electronic components (like transformers, capacitors) and in composite materials requiring high thermal stability.
Case Study 1: Guardians of Electronics
Imagine the densely packed electronic components inside a high-end server. They generate significant heat during operation and demand exceptional electrical performance. Using Methyltetrahydrophthalic Anhydride (MeTHPA) as the epoxy hardener for potting creates a protective layer with a high Glass Transition Temperature (Tg > 150°C / 302°F) and superb dielectric properties. This ensures components operate reliably even under harsh high-temperature, high-voltage conditions, significantly enhancing equipment lifespan. Industry analyses estimate that proper encapsulation can reduce electronic component failure rates by over 20% (Source: Electronic Packaging Materials Industry Analysis).
Phenolic and Other Types of Curing Agents
- Phenolic Curing Agents: Represented by phenolic resins (e.g., phenol-formaldehyde resins). They react with epoxy resins to form ether linkages. Cured products offer good heat resistance, chemical resistance, and dimensional stability. Often used in molding compounds and laminates.
- Latent Curing Agents: These hardeners can be mixed with epoxy resin at room temperature and exhibit a long storage life (pot life). They only become active and initiate curing under specific conditions, such as heat, light, or pressure. Examples include Dicyandiamide (DICY) and imidazole derivatives. They are ideal for one-component epoxy systems like powder coatings and single-part adhesives.
- Catalytic Curing Agents: These don’t significantly become part of the cross-linked network themselves but rather promote the polymerization of the epoxy resin or the reaction between other curing agents and the epoxy. Examples include tertiary amines, imidazoles, and Lewis acids.
- Other Types: Include thiol (mercaptan) curing agents (for fast, low-temperature cure), cationic curing agents (UV or thermal cure), etc., meeting specific application demands.
Making the Right Choice: Key Factors Influencing Epoxy Hardener Selection
Selecting the appropriate epoxy resin curing agent is a critical decision involving multiple factors. The wrong choice can lead to incomplete cure, subpar performance, or even product failure. Here are the core considerations:
- Reactivity and Curing Profile: This directly impacts the curing speed, pot life (working time), and required cure temperature/schedule. Fast cure suits production lines, while long pot life facilitates working with large parts. Selection depends on process requirements and available equipment.
- Heat Resistance (Thermal Stability): Determined by the hardener type and the resulting cross-linked structure. Often characterized by the Glass Transition Temperature (Tg). A high Tg means the material retains its mechanical properties and dimensional stability at higher temperatures, crucial for aerospace, automotive under-hood, and other demanding applications.
- Mechanical Property Requirements: Is high strength and modulus needed, or is flexibility and impact resistance more important? Different hardener systems impart different mechanical characteristics. For example, some long-chain modified amine hardeners can improve toughness.
- Chemical Resistance: Will the application environment involve exposure to solvents, acids, bases, or other corrosive substances? Aromatic amine and acid anhydride systems generally offer superior chemical resistance.
- Electrical Properties: For electronics applications, dielectric constant, dissipation factor, volume resistivity, and dielectric strength are critical. Acid anhydrides often excel here.
- Toxicity and Environmental Friendliness: With increasing environmental regulations (like REACH in Europe) and focus on occupational health, low-toxicity, low-odor, and low-Volatile Organic Compound (VOC) eco-friendly hardeners are gaining prominence. Choosing products compliant with regulations and safer for workers and the environment is essential.
- Color and Appearance: For coatings, flooring, and decorative applications, the color, clarity, and yellowing resistance of the cured system are important. Cycloaliphatic amines often provide good color stability and weather resistance.
- Cost and Availability: Prices can vary significantly between different types of hardeners. A balance between performance requirements, cost-effectiveness, and reliable supply chain is necessary.
Applications Everywhere: Where Epoxy Resin Curing Agents Shine
Thanks to their adjustable properties and broad applicability, epoxy systems powered by the right epoxy resin curing agents are vital in numerous sectors:
- Construction:
- Flooring: Provides wear-resistant, chemical-resistant, easy-to-clean surfaces for factories, garages, commercial spaces.
- Structural Adhesives: Used for concrete crack repair, rebar anchoring, bonding precast elements; offers high strength and durability.
- Anti-Corrosion Coatings: Protects steel structures, tanks, and pipelines from corrosion.
- Grouting Materials: Used for secondary grouting of equipment bases, structural strengthening.
Case Study 2: Accelerating Infrastructure Renewal
Modern bridge construction or repair projects often need completion within tight timelines to minimize traffic disruption. Structural adhesives or grouts formulated with fast-curing modified amine epoxy hardeners can achieve sufficient strength in hours, or even minutes, allowing traffic to resume much sooner. For instance, an emergency repair project on a city overpass used rapid-cure epoxy mortar, reducing the planned 3-day repair time to just 18 hours, significantly lessening the impact on commuters (Source: Municipal Engineering Report).
-
Electronics and Electrical:
- Potting and Encapsulation: Protects sensitive components from moisture, dust, vibration, and chemicals; provides electrical insulation.
- Laminates: Base materials for manufacturing Printed Circuit Boards (PCBs).
- Conductive/Thermal Adhesives: Used for chip bonding, heat dissipation management.
- Insulating Varnishes: For motor windings, transformer coils.
-
Composite Materials:
- Aerospace: Manufacturing aircraft fuselage, wings, tail sections; requires lightweight, high strength, high-temperature resistance.
- Wind Energy: Fabricating massive wind turbine blades.
- Automotive: Body panels, structural components, drive shafts for lightweighting.
- Sporting Goods: Fishing rods, tennis rackets, bicycle frames.
-
Coatings:
- Marine and Offshore: Provides excellent corrosion protection.
- Container Coatings: Weather, abrasion, and chemical resistant.
- Pipe Coatings: Internal and external anti-corrosion.
- Powder Coatings: Eco-friendly, efficient, widely used for appliances, metal furniture, automotive parts.
-
Adhesives:
- Structural Adhesives: High-strength bonding of metals, ceramics, composites in automotive, aerospace, construction.
- General Purpose Adhesives: For bonding and repairing various materials.
Looking Ahead: Future Trends in Epoxy Resin Curing Agents
To meet growing market demands and stricter environmental regulations, epoxy resin curing agent technology is advancing in several key directions:
- Environmental Friendliness (“Greening”): This is paramount. Developing and utilizing low-toxicity, non-toxic, low/zero-VOC hardeners is the main trend. This includes waterborne hardeners, bio-based hardeners (using renewable resources like vegetable oils), and formulations free from hazardous substances (e.g., nonylphenol-free). The market share for eco-friendly hardeners is projected to grow by over 40% by 2030 (Source: Chemical Market Research).
- High Performance: As applications demand ever-higher material performance (e.g., higher service temperatures, improved toughness, faster cure cycles), developing high-performance hardeners with increased Tg, better fracture toughness, faster reactivity, or longer pot lives remains a continuous focus of R&D.
- Multi-functionality: Future hardeners won’t just cure; they’ll impart additional properties. Developing multi-functional hardeners with inherent flame retardancy, electrical conductivity, thermal conductivity, self-healing capabilities, or antimicrobial properties can simplify formulations and enhance product value.
- Intelligence (“Smart” Curing Agents): This is a cutting-edge direction. Research is exploring intelligent hardeners that respond to external stimuli (like light, heat, moisture, pH) to control their curing behavior or properties. Imagine a hardener that activates only when needed or automatically adjusts its cure speed based on ambient temperature – this could revolutionize manufacturing processes. How might this change the way we build things?
Conclusion: Choose the Right Epoxy Hardener, Unleash Material Potential
While only one part of the epoxy system, the epoxy resin curing agent plays a critical role, profoundly influencing final product performance and application suitability. From understanding its basic principles and chemical reactions, familiarizing ourselves with its diverse classifications and properties, to mastering the key selection factors and appreciating its vast application areas, it’s clear that selecting and using the right epoxy hardener is paramount to developing high-performance epoxy materials.
As technology advances, environmental friendliness, high performance, multi-functionality, and intelligence will continue to shape the future of epoxy resin curing agents, bringing even more innovative possibilities across industries.
Are you searching for the ideal epoxy resin curing agent for your project?
We possess years of expertise and offer an extensive product line covering various types of epoxy hardeners to meet your diverse needs in construction, electronics, composite materials, coatings, adhesives, and more.
- Need product recommendations based on specific performance requirements (e.g., high heat resistance, fast cure, low toxicity)?
- Looking for a specific CAS number hardener or an alternative?
- Have questions about the application or formulation of a particular curing agent?
Contact our technical experts today! We are ready to provide professional consultation, detailed product information, and tailored solutions. Send us your inquiry, let us help you find the perfect epoxy resin curing agent for your application, and let’s drive your project’s success together! [info@sinocurechem.com]